F1レーシングチームのマクラーレンがストラタシス社の3Dプリンターを活用し新しいパーツを製造
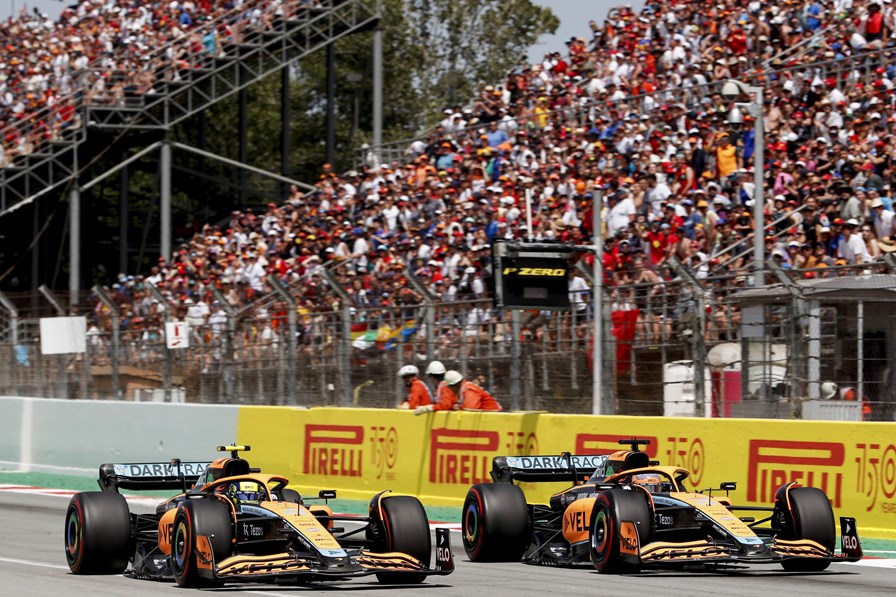
累計180回以上のグランプリ優勝を遂げ、F1史上最も成功したチームの一つであるMcLaren(マクラーレン)が、産業用3Dプリンターメーカー ストラタシス社の3Dプリンター「Neo800」を5台用いて年間最大9,000個のパーツを3Dプリントしていることが、ストラタシス社の発表により分かった。(画像はMcLarenのF1マシン。出典:Stratasys社)
3Dプリンターで厳しい競争に対応
F1のレース車両では、1gや1μmといったほんのわずかな設計の見直しが勝敗や順位を大きく左右する。McLarenはそのような過酷な競争環境に対応し、卓越したマシンをつくり出すためにStratasys社の3Dプリンター「Neo800」を導入した。F1マシンはスピードや耐久性の向上のために、何度も設計を新しくしていく。Neo800は最終的に完成するマシンのパーツ作製だけでなく、プロトタイプをつくりあげるのにも大きく貢献しているという。

3Dプリンター「Neo800」 出典:Stratasys社
F1マシンはダウンフォースの増強や空気抵抗低減のために、巨大な扇風機のような物で人工的に風を発生させて、空気の流れを確認する風洞試験を行い、改良を重ねていく。McLarenでは60%サイズのスケールモデルを何度も作製して、風洞試験を繰り返すが、ここで金型を必要としない3Dプリンターを活用することで時間と費用を大きく削減することに成功した。Neo800 の導入により、McLarenは自社拠点でスケールモデルを1から製造できるようになり、下請け業者とそれに伴う品質保証のコストも削減できたという。
Neo800は、風洞試験に使用するスケールモデル用に開発された特別な樹脂「Somos® PerFORM Reflect」を素材に、フロントウィングとリアウィングのプログラム、およびサイドボディワークの大きな部分のための数千のパーツ製造に使用されている。

「Neo800」で3Dプリントされたエアロパーツ一式。 出典:Stratasys社
McLarenのアディティブ・マニュファクチャリング部門の責任者であるTim Chapman氏はのNeo800導入の効果について、以下のように述べている。
「新しいNeoシリーズの3Dプリンターは、当社の空力風洞部品やプロジェクトのリードタイムを劇的に短縮するのに役立っています。Neo800の大きなベッドサイズにより、非常に大きなパーツを迅速に、しかも非常に高いレベルのディテール、精細度、再現性で造形することができます。Neo800で製作した高精細な部品は、手仕上げを最小限に抑えることができ、風洞試験の効率や、パーツの仕上げにかかるサイクルタイムが劇的に短縮されました」
従来以上のものを作るために活用される3Dプリンター
3Dプリンターを用いることで、製造にかかる時間の効率化や、コストカットにつなげることができる。また、高性能部品の少量生産の特注部品の製造には3Dプリンターは適している。従来の工法では作ることが困難だったものを新たにつくり出すためにも3Dプリンターの導入が活発になっている。
3Dプリンターは自動車業界との親和性が高く、さまざまなメーカーでの活用が広がっている。以下に関連記事をまとめてあるので、そちらもぜひご覧いただきたい。
https://news.sharelab.jp/?s=%E8%87%AA%E5%8B%95%E8%BB%8A
国内外の3DプリンターおよびAM(アディティブマニュファクチャリング)に関するニュースや最新事例などの情報発信を行っている日本最大級のバーティカルメディアの編集部。