製造時間が2週間から2時間に短縮!DMG森精機社が新型大型金属AMハイブリッド機を初公開
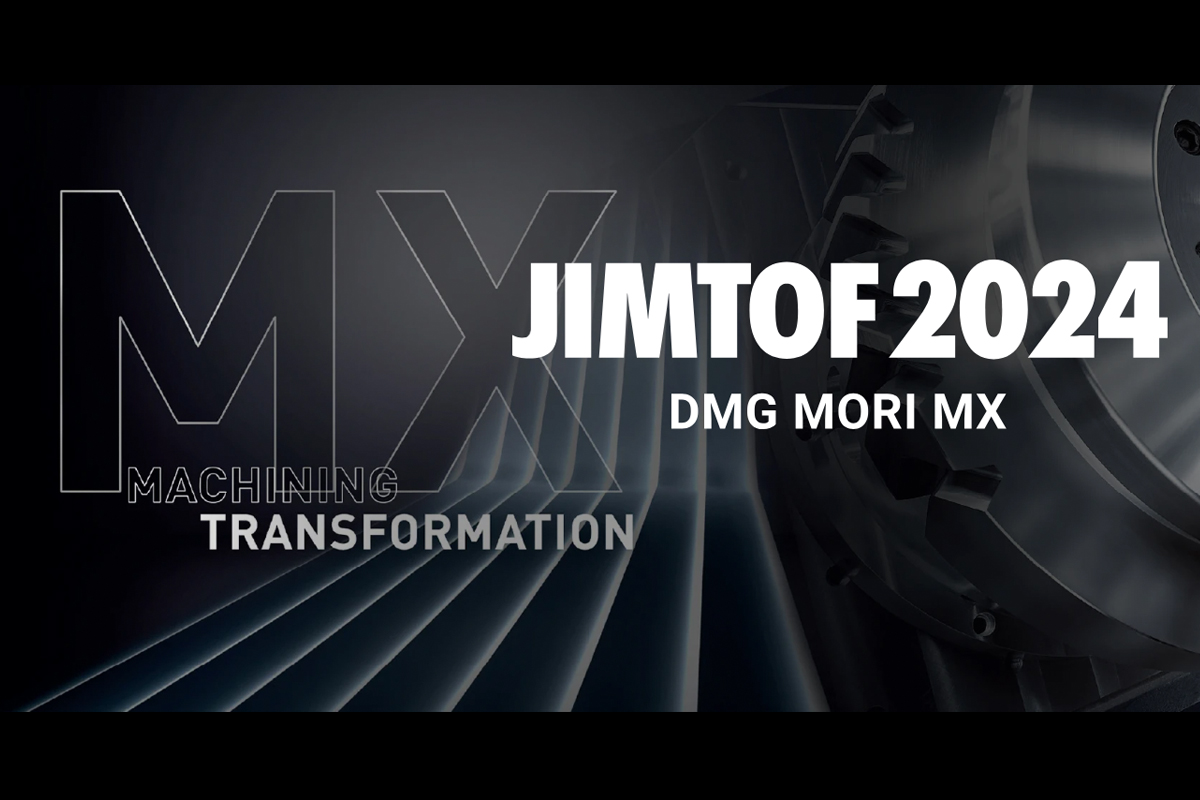
DMG森精機社(東京都江東区)は、新型のハイブリッド金属積層造形機「LASERTEC 3000|3000 DED hybrid 2nd Generation」を発表した。この機器はパウダーノズル(DED)方式の金属積層造形機能と複合加工機の切削機能を統合した「LASERTEC DED hybrid」シリーズの最新モデルである。最大加工長さは3,018mmで、大型シャフトロールのような大型ワークの加工にも対応可能で、2024年開催の第32回日本国際工作機械見本市JIMTOF2024において初めて世界に公開された。(上部画像はDMG森精機社JIMTOF特設サイト。出典:DMG森精機社)
「LASERTEC 3000|3000 DED hybrid 2nd Generation」
DMG森精機社が新たに発表した金属積層造形(AM)と切削加工を一体化した工作機械「LASERTEC 3000|3000 DED hybrid 2nd Generation」は、大型部品の製造に特化し、複雑な形状を高精度で造形する能力を持つ。従来の加工工程では、金属積層造形後に別工程で切削加工が必要だったが、この装置では両者をシームレスに連携させることで、製造時間の大幅な短縮を実現している。
さらに特長としては、積層造形と切削加工を同じプラットフォームで行う点にある。レーザーを使用した金属粉末の溶融積層により、複雑な形状を短時間で形成する一方で、切削加工によって表面の仕上げや寸法精度を高めることが可能で、また、装置内のモニタリング技術により、リアルタイムで造形プロセスの品質を管理できる。この統合アプローチは、工程間の搬送時間を削減するとともに、高品質な製品を安定的に供給できる。
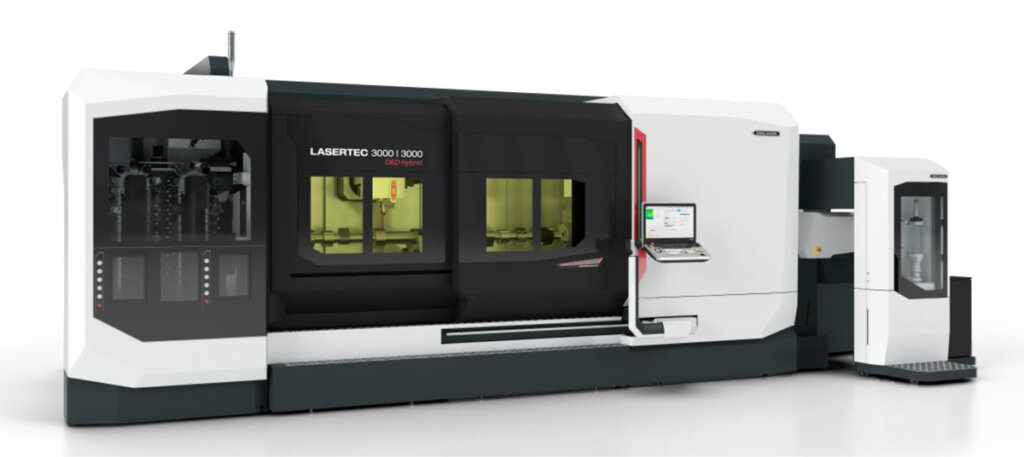
金属AMが実現する、従来工法を超える効率と環境性能
従来の加工法では、粗加工を施した後、焼き入れや焼き戻しを行い、熱ひずみを除去した上で、硬質クロム(Cr)メッキを施し、最後に仕上げとして研削を行う必要があった。これに対し、金属AM技術を活用する新たな製造方法では、母材として一般的な炭素鋼「S45C」を使用し、その表面に約1mmのハイス鋼を積層造形することで対応する。このプロセスにより、硬度HRC65以上を達成し、焼き入れ工程で得られる硬度を超える性能を実現した。また、500万回に及ぶ摺動試験もクリアしている。これにより、焼き入れなどの熱処理や外部委託による硬質クロムメッキ処理が不要となり、工期の大幅な短縮が可能となった。
さらに、製造工程の効率化に伴い、リードタイムが短縮され、材料費も削減されることで、製造コストを従来比で約8割削減できるとされている。また、温室効果ガスの排出削減や、硬質クロムメッキを使用しないことによる環境負荷の軽減にも寄与するとしている。この技術は、2025年以降、同社の工場で採用され、主軸搭載用のドローバーの製造に活用される予定である。
期待される導入効果
この装置の導入により、製造コストと時間の大幅な削減が期待される。従来は2週間以上かかっていた工程が、わずか2時間で完了することは、製造現場にとって大きな利益をもたらす。また、積層造形と切削加工を一体化することで、設計の自由度が向上し、より複雑な部品の製造が可能となる。さらに、リアルタイムモニタリング技術の活用により、品質管理が効率化され、歩留まり率の向上も見込まれる。これらの効果は、生産性の向上に直結する。
DMG森の関連記事
今回のニュースに関連するものとして、これまでShareLab NEWSが発表してきた記事の中から3つピックアップして紹介する。ぜひあわせてご覧いただきたい。
国内外の3DプリンターおよびAM(アディティブマニュファクチャリング)に関するニュースや最新事例などの情報発信を行っている日本最大級のバーティカルメディアの編集部。