ポルシェ、3Dプリンターを活用した電気ドライブのハウジングを製造
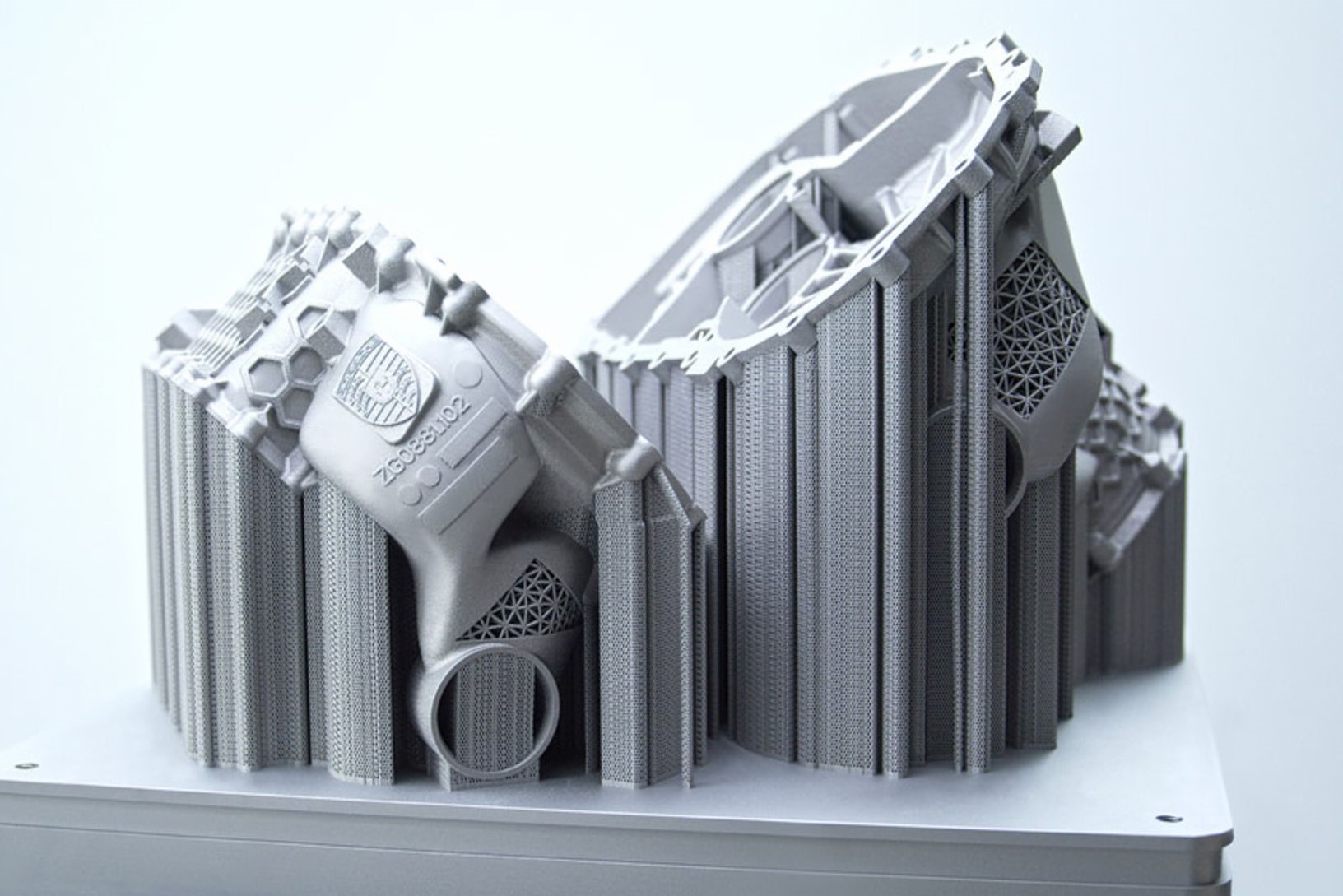
ポルシェは、3Dプリンター技術を活用し電動ドライブのハウジングを製造したことを発表した。同社によれば、従来の製造(鋳造)部品と比べ10%軽量で、剛性が高いため、軽量かつ過酷な状況下でも耐えうる自動車に適しているとのこと。
今回はポルシェが当たらに開発した電気ドライブハウジングの特徴と、3Dプリンティング技術を積極的に活用しているポルシェの活用事例についてご紹介する。
目次
3Dプリンターで実現した軽量×強度×品質向上
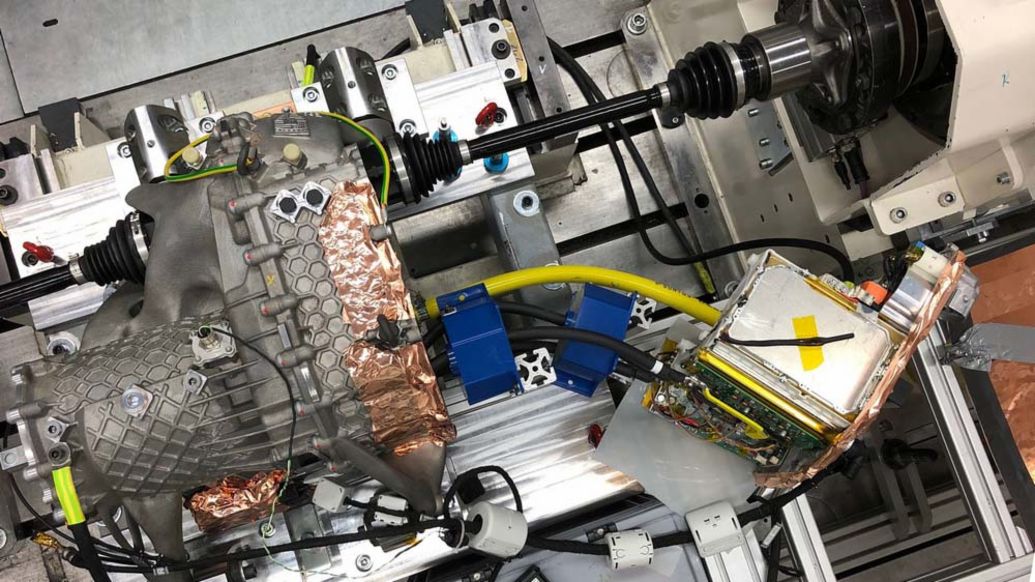
今回開発されたハウジングは、従来の鋳造部品よりも軽く、全体として10%の重量削減を達成したうえで、3Dプリントによってのみ実現可能な構造とすることで、高応力領域の剛性が2倍になった。また、多くの機能や部品が統合できることで組立作業も大幅に削減され、さらに部品の品質向上にも直結するのも利点としてあげられる。
今回の開発には多くの課題があった。例えば、3Dプリンターにより提供される設計の自由度は特定の設計要件とも密接に関連しており、ワークピースが融合によりレイヤーごとに生成されるという事実を考慮したうえで、設計段階でレイヤーが構築される方向を予め考慮しなければならない。
しかし、現在利用可能な機械技術ではプロセスが多く複雑であったため時間がとられていた。それが最新世代の機械では、この時間を90%短縮することが可能であり、ハウジング全体をひとつのプロセスで製造できるようになった。
そのため、ハウジングの重量は約40%削減(これはドライブユニット全体として見た場合には約10%の軽量化を意味する)され、同時に剛性が大幅に向上した。また、部品の統合によりドライブユニットがよりコンパクトになり、ドライブパッケージが大幅に改善され、組み立て作業が削減されることで、生産時間を約20分短縮した。
追加の利点として、ギアボックス熱交換器と最適化された熱伝達の統合により、ドライブ全体の冷却が向上する。これはパフォーマンスをさらに向上させる要件となる。
ポルシェ開発センターのパワートレイン先端開発部門のプロジェクトマネージャーであるフォーク・ハイルフォート氏は「電気的に高負荷を受ける部品にも適しており、例えば限定生産のスポーツカーに使用される」と述べている。
少量部品の開発・製造を可能にする3Dプリンターの推進
SlaleLab編集部でも以前ご紹介したが、3Dプリントされたピストンが『911 GT2RS』高性能スポーツカーに採用され、その信頼性を証明している。
開発されたドライブのハウジングも高い品質要件を満たし、ポルシェによるすべての品質・ストレス試験をクリアしている。ハウジングはモーターと2速のギヤボックスを統合したもので、スポーツカーのフロントアクスル用に使用される。パワートレイン先進開発プロジェクトのマネージャー Falk Heilfort 氏は、開発目標について「我々の目標は、付加製造技術の可能性を秘めた電動ドライブを開発すると同時に、ハウジングにできるだけ多くの機能と部品を統合して重量を減らし、構造を最適化することだ」と述べている。
3Dプリンター技術を活用したポルシェの実績
ポルシェは今までも3Dプリンター技術を活用して多くの実績を出してきた。
例えば、自動車のシートの中央部分、背もたれのクッションの一部が3Dプリンターで製造している。将来的に顧客は、自動車の購入時に中央パーツの硬さを3種類(ハード、ミディアム、ソフト)から選べるようになるという。それぞれのレーシングドライバー向けにパーソナライズされた専用バケットシートは、顧客のニーズを満たす製品となっている。
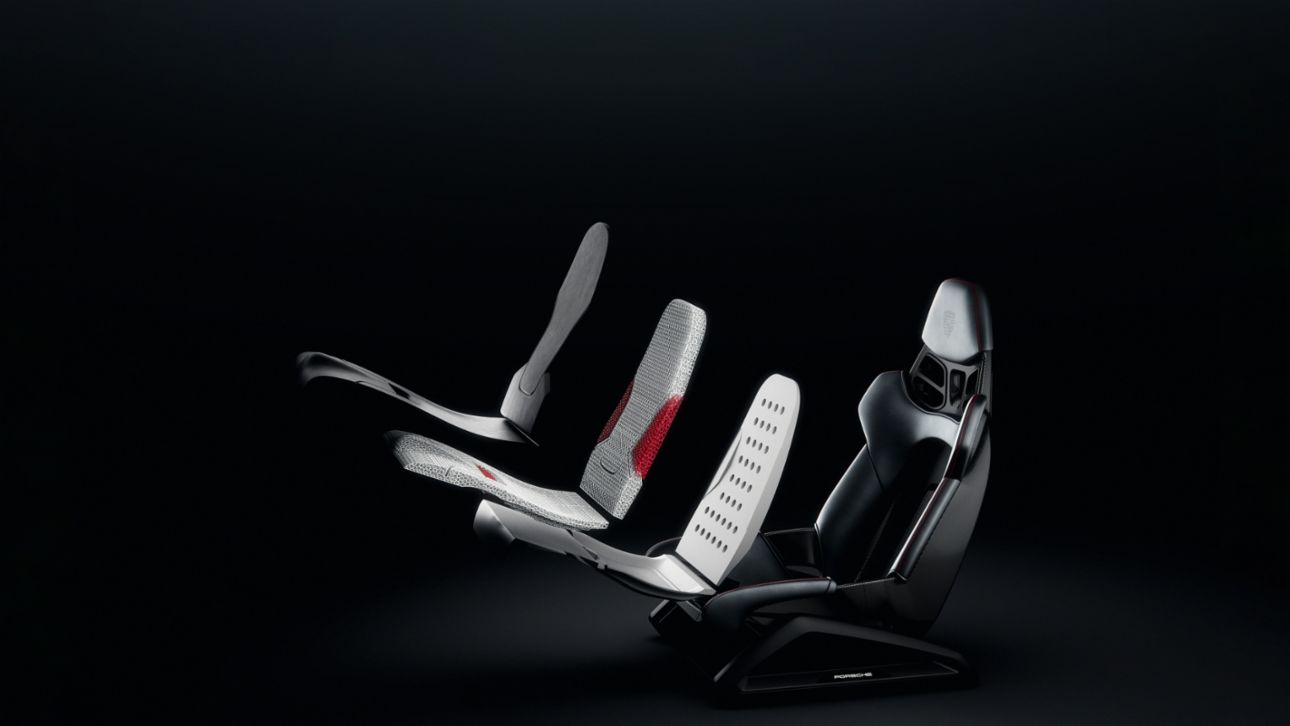
また、ポルシェでは少量部品の開発に適している3Dプリンターの特徴を活かし、クラシックカーの部品を製造している。ポルシェクラシックシリーズには現在、約52,000のパーツが含まれており、特定のスペアパーツの在庫がなくなった場合、元のツールを使用して再現される。しかし、非常に限られた数でしか必要とされないスペアパーツの供給を確保することは非効率で難しい問題でだった。そこで、ポルシェは20のパーツを3Dプリンターで製造することで効率的かつコストを抑えて提供できるようになった。
今回、電気ドライブハウジングの開発により、3Dプリンターの新たな可能性を示すことに再び成功した。そしてプロセス革新の分野や、スペアパーツ、カスタマイズなどの新しいビジネス分野における可能性も広がっている。今後もポルシェの動向には目を離せない。
関連情報
自動車業界で活用される3Dプリンター
3Dプリンターの繊細で創造性豊かなところに惹かれます。そんな3Dプリンターの可能性や魅力を少しでも多くの人に伝えられるような執筆を心がけています。