3Dプリンターで2年間に200種類以上の治具を開発したEIZOから学ぶ4つのポイント

目次
新規製造ラインの立ち上げのタイミングでCarbon社の3Dプリンター導入を決めたEIZO株式会社。導入から2年の間に200種類以上の治具を製作してきたという。実際に製造ラインや製作した治具を拝見しながら、陣頭指揮をとったEIZO株式会社製造部 生産技術課の専 雅晴氏にお話をお伺いした。
実際のラインや治具をご紹介いただき、一つ一つの工程やそこでの治具の使い方、製作の工夫などを丁寧にご説明いただいたので、これから治具を3Dプリンターで内製化しようとご検討の方は、ぜひご一読いただきたい。
(聞き手:シェアラボ編集部、語り手:EIZO株式会社 製造部 生産技術課 専 雅晴氏、提供:JSR株式会社)
EIZOが作るハイエンドなモニター製品群
―EIZOさんはデザイナーが使うハイエンドなモニターを製造されている印象があります。
そうですね、EIZOでは一般的なモニターだけでなく、色の再現性が高いカラーマネージメントモニター、産業分野向けや医療機関向けモニターなども製造しています。
カラーマネージメントモニター 医用画像表示モニター
本社工場(石川県)
本日お越しいただいた本社工場では主に少量多品種生産に取り組んでいまして、私たちの生産技術部門では、新しい生産方式の検討から設備の導入や改善を担当しています。
導入のきっかけは製造ラインの新設
―少量多品種生産となると、生産技術の方への生産準備の負荷も高そうですね。Carbon社の3Dプリンターを導入した目的は治具製作だとうかがっていますが、直接のきっかけは何ですか?
専用ロボットハンド 固定治具
以前は治具を自分たちで設計して、加工は外注することが多かったのですが、Carbon社のM2より以前に導入したFDM方式の3Dプリンターで治具製作をおこない一定の手ごたえを感じていました。そんな中で新規製造ラインの立ち上げがありまして、このタイミングで3Dプリンターの利用範囲を拡大しようと考え、Carbon社のM2プリンターを導入しました。
製品設計部門が先陣を切ってというわけではなく、生産の際に使う治具などに焦点を当て、導入効果を想定して導入している点が他のCarbon社の事例と違うところかもしれませんね。
2年で200種類以上の治具を製作
―導入して2年でどのくらいの治具を製作されましたか?
そうですね、ざっと200種類以上製作しました。少量多品種生産に取り組んでいますので、新しい製品が起こると、生産用の治具も必要になります。いままでのFDM方式の3Dプリンターは造形に失敗することもあれば、製作にも時間がかかったので、一部にしか活用できていませんでしたがCarbon社のM2プリンターは造形が安定していて、以前に使っていたFDMよりかなり高速です。活用の範囲は広がっています。
―どんな治具をつくってきたか、いくつかご紹介いただけますか?
ここに並んでいる治具がそうなんですが、コストパフォーマンスが大きく改善できたのが、こちらの固定治具です。
医用画像表示用モニターの製造で
活躍する固定治具
この固定治具は1セット分など、必要なだけしか製造しないこともあって、今まではアルミのブロックを両面削り出して業者さんに加工してもらっていました。そのため費用もそれなりに高く、一つ数万円程度の費用が掛かっていました。これがCarbon社の3Dプリンターで造形すると一つ千円もしません。かなりのコストダウンを実現できています。
―非常に大きなコストダウンですね!
コストも大きく削減できましたが、調達にかかる時間も大きく短縮できています。納品されるまで2週間から3週間はかかっていた固定治具が数日以内に内製できます。失敗したらまたやり直せるという点で安心感もあります。
―内製ならではのメリットですね。造形は専門の造形者の方が行いますか?それとも設計される方がそのまま造形も担当していますか?
設置されているM2プリンター。光で形を造形。 有機溶剤で洗浄。空調も万全の作業台。 エアーで吹き、右の熱処理機で強度を出す。
設計者が直接造形も行います。いま10人以上が使っていますが、自分が設計し、自分で造形します。プリンターから取り出し、洗浄後に熱処理を行うところまで自分の作業で行います。治具製作のためにしか使っていませんが、いま週4日はなんらかの形で稼働している状況です。
―かなりの稼働率ですね。それに設計者が自分で造形まで行うと、3Dプリンターを使った造形の実際のところも把握できて設計しやすくなりますよね。
自分で設計から3Dプリンターでの造形までやってみて、治具製作が非常に楽になりました。というのも、設計上の制約がほとんどないんです。金型で作ってもらう際に気を付けなければいけないことは、3Dプリンターで作れば、全く意識しなくてもモノが作れます。このロボットハンドは、カメラなどのセンサー類をロボットアームに固定するために用意しているのですが、設計的には非常にシンプルです。
検査用ロボットのハンド部
固定するセンサーやカメラのサイズと固定金具を止めるビス穴をあけて、アームに固定する穴をあけてという形で、やりたいことをそのまま形にしているだけなんです。設計にかかる期間も他の工法にくらべて非常に短く済んでいます。
―工法に縛られていた設計の制約がなくなったということですか?
そうですね。本当にこの部品は作れるのか、と考える必要はないですね。どんな形状でもモノがつくれてしまうので。逆に私たちは「3Dプリンターならではの設計」にはあまり取り組んでいません。社内で使う治具なのでそこまで凝る必要がないといいますか、必要な機能と形状を備えた治具が、現状でも早く安く用意できるので、目的としては達成できているんですよね。
―なるほど。そんな中で何度も試行錯誤した治具はありますか?
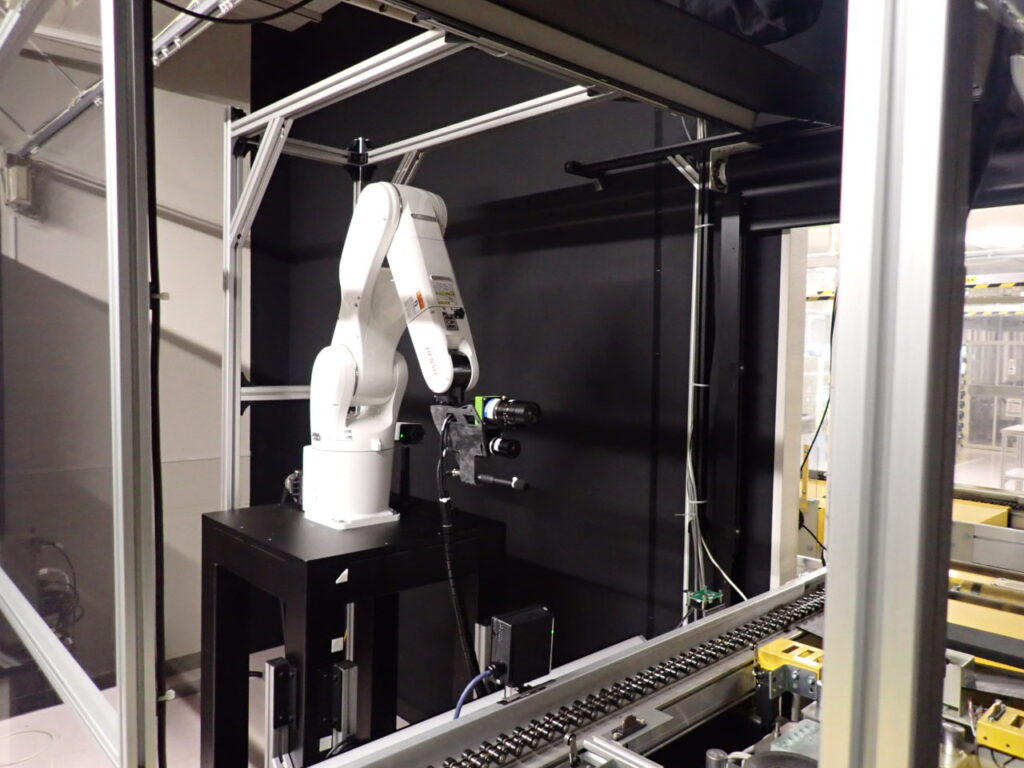
先ほどご紹介したロボットハンドは試行錯誤を繰り返しました。ロボットハンドは市販の部品もあるのですが、大半の場合、改良が必要になります。今回は完成したモニターの検査の一部を自動化するためにカメラやセンサーをハンドに取り付けています。
検討を進める中で、カメラやセンサーの種類や距離を変更しながら進めて行くので、ロボットハンド部は変更を繰り返して、実際に製作して、動作を見ながら完成度を上げるというサイクルを繰り返します。Carbon社の3Dプリンターは設計制約が少なく造形時間も短いので通常よりも手間も少なく、短い時間で完成させることが出来ました。
―ここまでお話をうかがってきて、3Dプリンターが、かなり業務になじんでいるご様子が伝わってきました。
3Dプリンターを使うことは、私たちにとって当たり前になっています。逆に他の方法で調達できる物でも、手軽に作ることができるので、四角いブロック形状のようなものまで3Dプリンターで作ってしまいます。
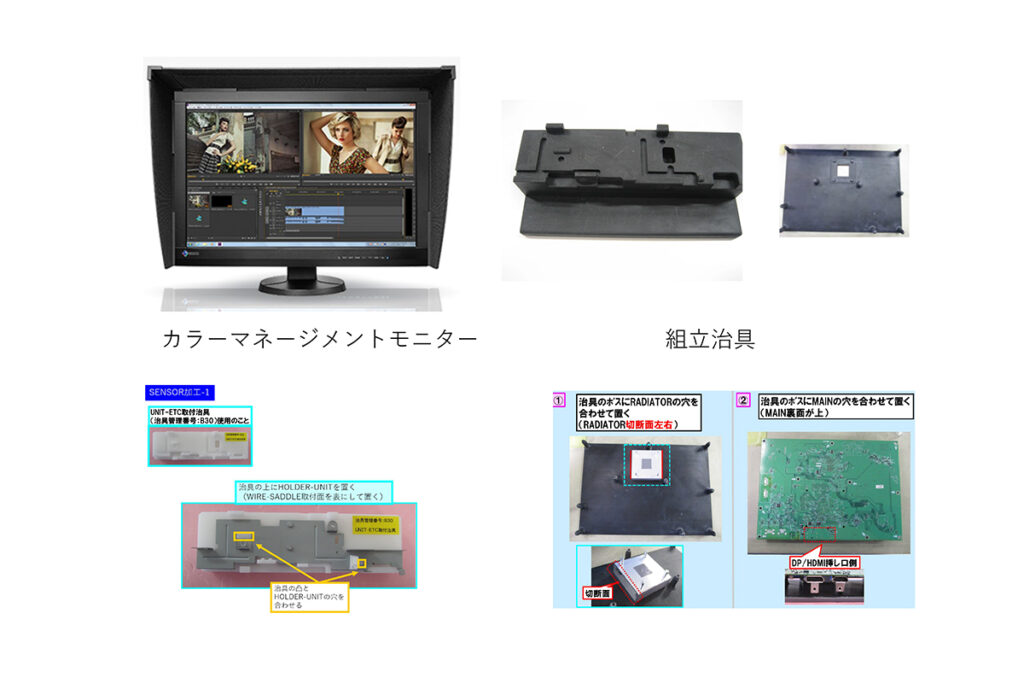
―3Dプリンターで製作する治具は1種類あたり、だいたい何個ぐらい用意するものですか?
少量多品種ラインのために新規製作する治具は、1セットから多くても数十個セットというのが多いです。ですが最も多く作ったのは300個ですね。
製品の指示書。RFIDタグでも管理 RFIDの誤検知防止のため高さを出す工夫
これはRFIDタグを製品の指示書と合わせておいておくためのカンバンなのですが、モニターの土台の上に置きます。モニターの土台には金属が使われているので、直接カンバンを置いただけでは、RFIDが誤検知されてしまうので、高さが必要だったんです。この治具は300個必要でしたが、以前のFDMの3Dプリンターでは5個を30時間かけて作っていました。それがCarbon社のM2では25個を9時間半弱で造形できます。
―単純に考えて16分の1の時間に短縮できたんですね、、すごい効率化です。
造形所要時間を16分の1に短縮
そうですね。いままで3Dプリンターの守備範囲は1個から数十個だとおもっていましたが、数百個の部品も用意できるということがわかって視野が広がりました。Carbon社の材料価格はFDM方式のフィラメントとそんなに大きく変わらないので、コストパフォーマンスは非常に良いと感じています。
ようやく現場の声に向き合える体制になった
―こうして実際に狙い通りの治具を自由に作れるようになって、周りからの反応はどうでしたか?リクエストなどでてきましたか?
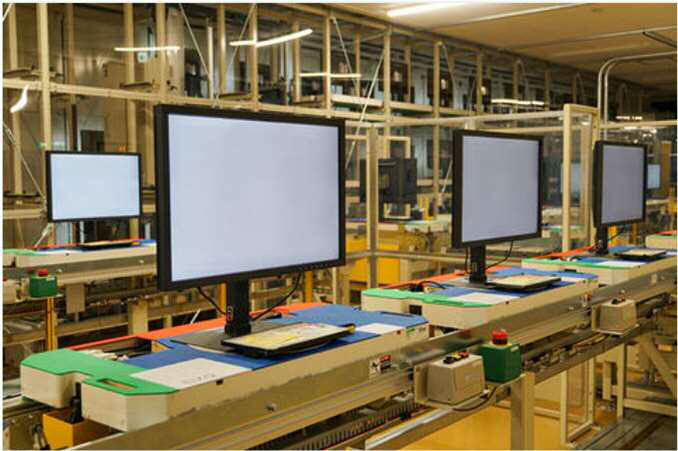
正直にお伝えすると、外注加工やFDM方式3Dプリンターでは、コストや時間がかかり過ぎて、現場の要望に応えられなかったことも多かったんです。ですがCarbon社の3Dプリンターを導入してから、コストも削減でき、時間にも素早く対応できるようになってきました。ようやく現場の声を拾って、タイムリーに改善していくことが物理的に可能になってきました。今まさに『現場の声に向き合えるようになってきた』というところです。
―少量多品種生産だと、生産期間も短いですもんね。今日拾った声を明日改善できるようになった。そんな大きな変化のように聞こえます。こうした現状での手ごたえを踏まえて、今後はどのような活用法をお考えですか?
製品の最終部品の製造にも活用していけたら面白いと思っています。3Dプリンターを活用しているのは生産技術部門が多いですが、製品設計部門でも活用していますので、メリットがあれば製品の最終部品への使用も考えています。
―従来の設計や製造の在り方で大きな問題がない場合は、取り組むのが難しいですよね。保守部品などから取り組まれるケースも増えてきていますが、EIZOさんの場合いかがですか?
いままでの考え方、やり方で最適化されているところを変えるのは、製品の最終部品ではいっそう大変だと思います。そういう意味でCarbon社のノウハウをもっと利用する機会があっても良いかなと思っています。
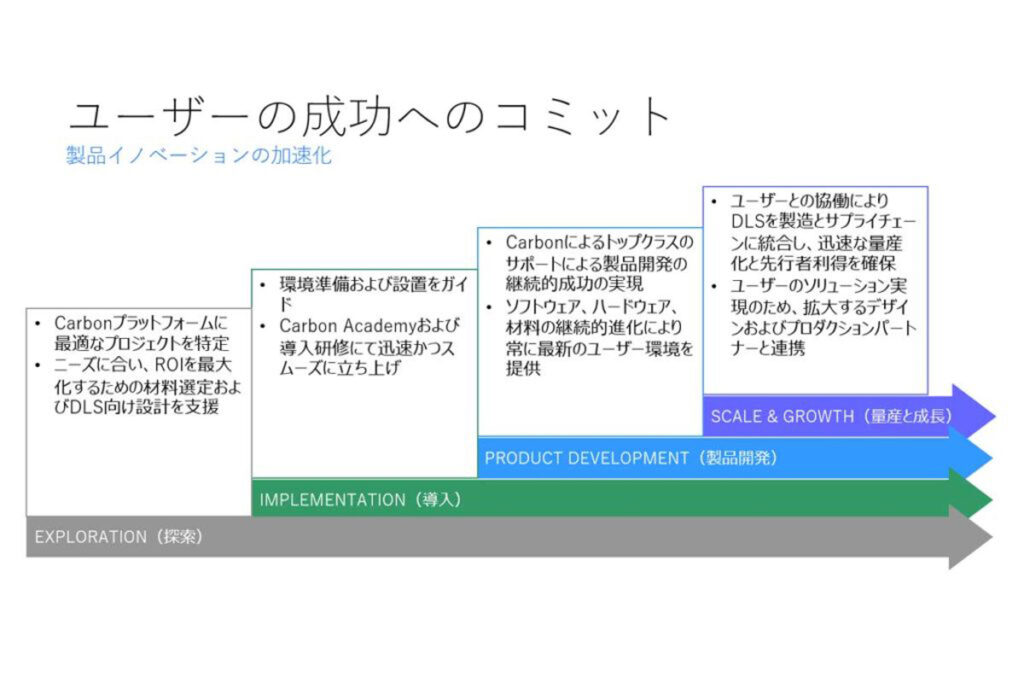
今回取材をお受けする前に、山本光学さんの事例記事を読んだのですが、その中でサブスクリプションの中で設計支援をかなり手厚く受けていることが紹介されていました。当社では利用する際にあまり困らなかったので、ほとんどCarbon社の設計支援を利用してきませんでしたが、こんな点が大きく改善できるなど具体的な変更点を、見える形にして支援頂いており、興味深い内容でした。
***
導入から担当したJSR銅木氏を交え、終始和やかな取材だったが、非常にオープンに製造現場も見学させていただき、気になるコスト削減効果に関しても具体的にご教示いただけた。これはEIZOが積極的に工場見学を受け入れる文化であることも大きいが、狙った導入効果がきちんと出ている手ごたえがあるがゆえだろう。次のページ以降では、専氏が語ってくれたEIZOの実例を取材する中で見えてきた「なぜ順調に3Dプリンター活用が現場に浸透できたか」に関してあらためて整理してみたい。そこには4つほどポイントがあるように思われる。次のページで詳しく見ていきたい。