BWT Alpine F1 チームが3Dプリンターを4台増設、年間 25,000 個の部品を生産可能 ― 3D Systems
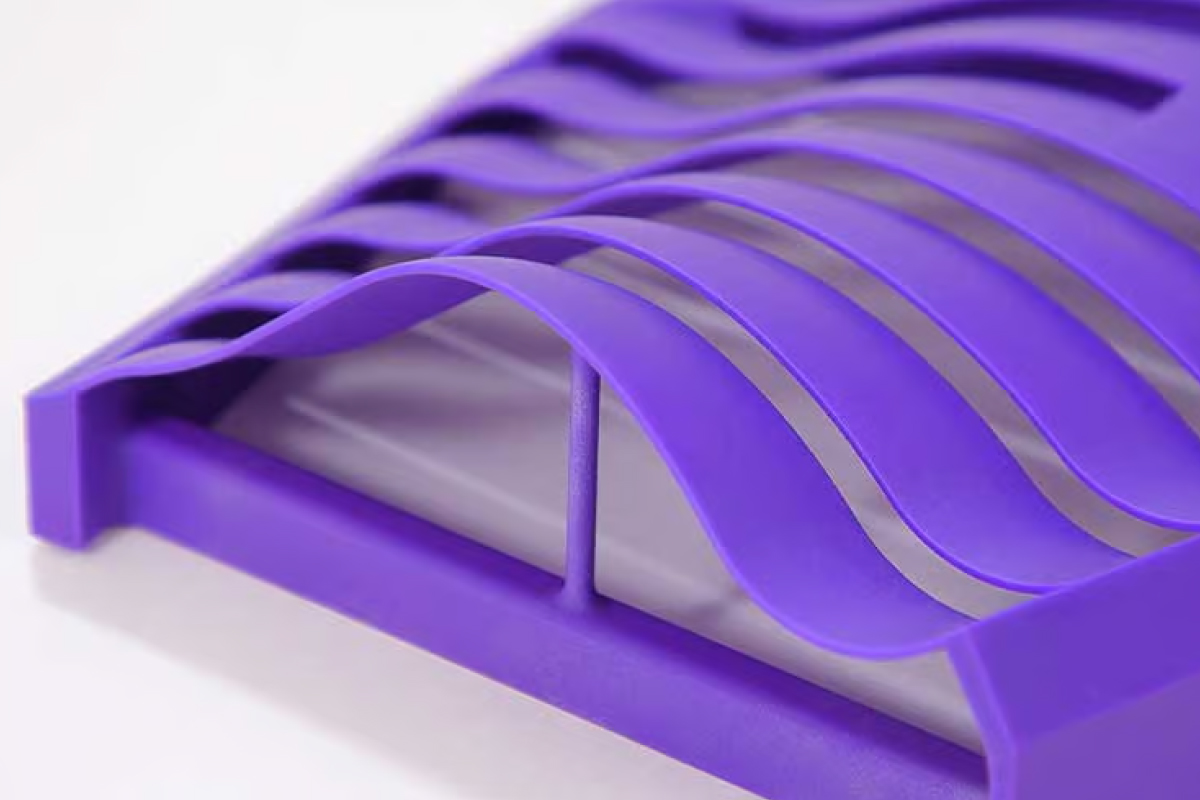
BWT AlpineのF1 チームが、風洞実験の最適化を図るためにSD Systemsの3Dプリンター(SLA方式)を4台増設した。同プリンターで風洞実験用のモデルを作成し、リードタイム削減とコストダウンに成功した。BWT Alpine F1チームは、今回の増設で年間で2万5000点ものAM部品を造形することができる。
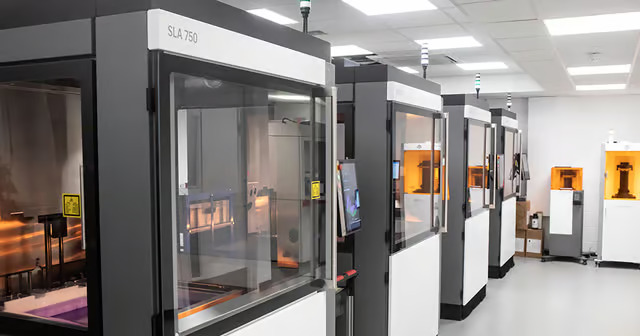
デザイナーと設計者の共通理解を生み出すための風洞実験
風洞実験とは、人工的に発生させた風のなかに対象物を置くことで、汚染源や環境濃度との関連を確認するために行うものである。デザイナーが感性的に描き出すスケッチをもとに、設計者が3次元CADでリアリティのある形状をデザインする。ソフトウェア上でシミュレーションを行ってすり合わせを行うことが日常的になってきたとはいえ、最終段階の詰めを行うためには、関係者を一同に集め、性能の可視化を行うことができる風洞実験は大きな役割を果たしている。
しかし、風洞実験を行うための模型をつくるためには製作工数が必要だ。削り出しなどの方法で製造していると、複数のバリエーションを効率的に比較検討できない。そこで3Dプリンターで造形されたモデルが活躍する。
風洞実験に最適な材料開発で検証工数を削減
風洞実験に使用する部品は、高コントラストかつ反射を抑えたものが求められる。ビデオカメラで撮影した際に、風の流れを可視化するために焚いたスモークが視認しやすくなるためである。また、試験の精度を高めるために、後加工で研磨や着色の工程が必要となる。
そこでBWT AlpineのF1 チームは、3D Systemsと材料を共同開発。高精度な風洞実験で用いられるPIV計測(粒子画像流速測定法)に最適な空力模型を作るための専用材料「Accura Composite PIV」を開発し、圧力タッピングを備えた複雑な空力部品、小型の複合ツール、高温結合用ジグなど、風洞試験用モデルを構築した。
引張強度72 MPa、曲げ弾性率9,500 MPaという硬さと粘りを期待できる材料を目指した。また熱硬化後の加熱たわみ温度: 100˚Cということで、連続して強い風圧を当てても試験ができる。 SLA方式に対応した液体材料として開発されていることもあり、複雑な形状でもなめらかな表面性を期待できる。
3Dプリンターの増設によって、造形時間と積層処理間の時間の短縮による生産性の大幅に向上し、また、ハイコントラストなカラーかつ、反射を抑えたなめらかな表面仕上げを可能になったことで、後処理と仕上げにかかる時間が短縮された。
BWT Alpine F1 チームは3D Systems の SLA 750がβ版としてリリースされた際からのテストユーザーとして、風洞実験での生産性を検証し、大きな手応えを掴んだということで、正式版リリース後に、導入台数を4台に増やしている。2023年3月時点で、毎年 25,000個の積層造形部品を製造するに至ったということだ。
自動車業界の関連記事
自動車業界の3Dプリンター活用に興味のある方は、以下の記事もあわせてご覧いただきたい。
国内外の3DプリンターおよびAM(アディティブマニュファクチャリング)に関するニュースや最新事例などの情報発信を行っている日本最大級のバーティカルメディアの編集部。