GE Aviationのシンガポール工場は、メンテナンス・修理・オーバーホール(Maintenance Repair Overhaul:MRO)に3Dプリンター技術を利用することに関し、世界で初めて承認を受けた。MRO分野にも3Dプリンターを活用することで、生産性の向上を目指す。
目次
航空産業で広がる3Dプリンターの活用
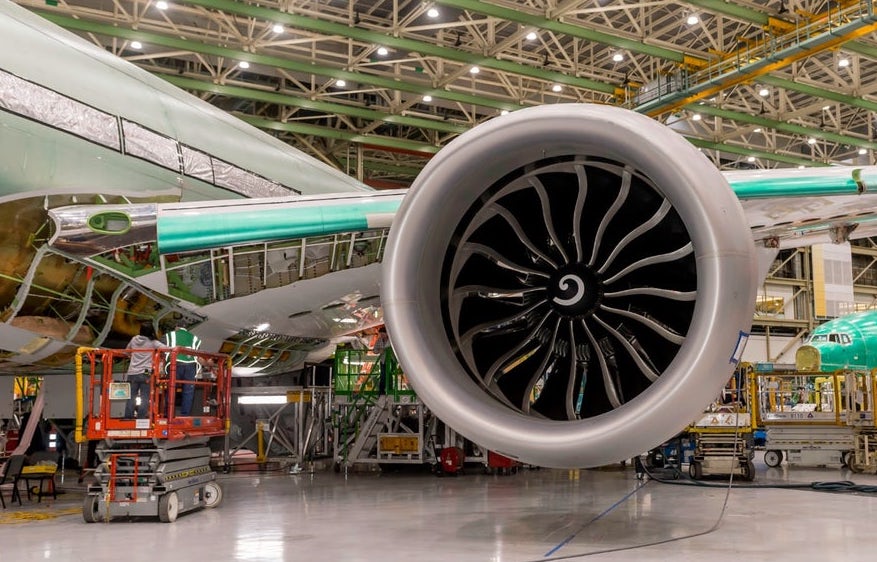
GE Aviationは、航空機のエンジンや電子機器、システムを提供する航空部品メーカーだ。GE90エンジンの開発に3Dプリンター技術を取り入れて以来、3Dプリンターの活用を積極的に推し進めてきた。
GE Aviation の3Dプリンター活用は、エンジンの試作・開発に留まらない。燃料ノズルチップを始めとした様々な部品の開発、そして、メンテナンスや修理の分野にも広がっている。
シンガポールのLoyangに位置するGE Aviationのメンテナンス・修理・オーバーホール(MRO)用施設は、修理に3Dプリンター技術を使うことに関して承認を受けたことで、世界初の「3Dプリンターを用いる MRO施設」となった。
MROに3Dプリンターを活用する利点
航空機のエンジン修理に3Dプリンターを活用することには様々な利点がある。
第一に、工期短縮による生産性の向上だ。
GE Aviation にメンテナンスを依頼する航空事業者各社にとって、メンテナンス期間の短縮は大きな利益を生む。これは、運航可能な航空機を実質的に増やすことになるためだ。
もちろん、GE Aviation側にとっても、メンテナンス期間の短縮は、人件費などのコスト削減につながる。
第二に、コンパクトなMRO施設を設計できる。
3Dプリンターの活用によって、必要な設備を減らすことができ、MRO施設の床面積を縮小することができた。
第三に、効率的な資源利用によって、持続可能なMRO事業が実施できる。
今後益々重要性を増す「持続可能性」について Managing Director である Iain Rodger氏は以下のようにコメントした。
「私にとって積層造形の重要な利点の 1つは持続可能性です。積層造形によって、より多くの部品を修理しつつも、より少ない廃棄物しか排出しません。利用するエネルギーを削減し、環境への影響を抑えます。修理工程は持続可能性について大きな役割を占めます。業界が拡大し、新しい技術が開発されるにつれて、修理工程の重要さは増していく一方です。」
活用事例:HPCブレード
GE Aviationは、修理工程における 3Dプリンターの活用例として、HPCブレードの修理を挙げている。
HPC(High-pressure compressor)とは、軸回転を圧縮空気に変換する部品を指す。簡単に言えば非常に強力な扇風機だ。いくつもの羽(ブレード)を有する HPC には、時間経過にとともに、様々な場所で、様々な損耗が生じる。故に、継続的な修理と交換が必要だ。
メンテナンスコストは膨大になり、かねてよりコスト削減が求められる分野だった。GE Aviationはこの分野で3Dプリンターの活用が大変有効であることを示した。
メンテナンスはまず、ブレード形状の 3Dマッピングと画像分析から始まる。続いて、画像分析結果を元にして、3Dプリンターが新しいブレードを製造するための指示プログラムを生成する。
状況に応じてカスタマイズされた指示プログラムを用いることで、修理箇所の部品製造に必要な資源、時間を削減可能だ。
Rodger によれば、「従来の修理プロセスと比較して、従業員が1日に2倍の部品を修理でき、生産性が向上した。後処理にも機器が不要であるため、必要な床面積を 2/3 に削減された」と述べている。
関連情報
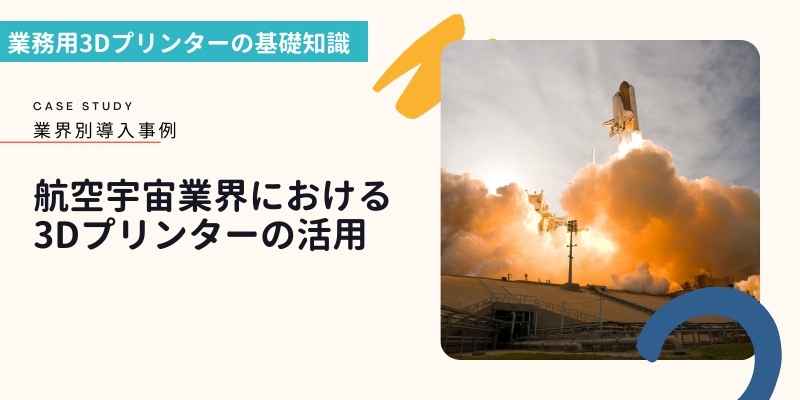
国内外の3DプリンターおよびAM(アディティブマニュファクチャリング)に関するニュースや最新事例などの情報発信を行っている日本最大級のバーティカルメディアの編集部。