造形方式とは、3Dプリンターが3Dモデルデータを実際に造形していく仕組みのことで、材料押出や結合剤噴射などさまざまな方法があります。造形方式の違いにより、適用できる材料や造形したモデルの精度、造形する際の速度などに違いがあるため、用途に応じた造形方式の選択が重要です。この記事では、3Dプリンターの造形方式の中でも、代表的な7種類について解説します。それぞれの造形方式が対応している材料や特徴を確認し、目的に合致する造形方式を見つけましょう。
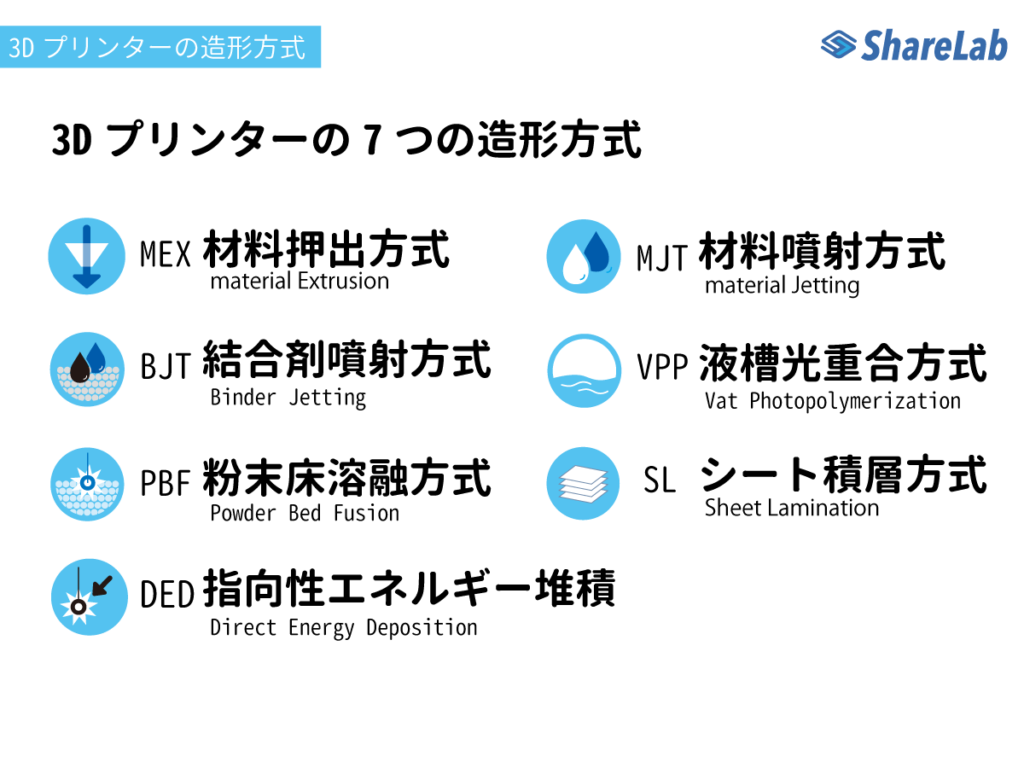
業務用3Dプリンターの造形方式
大きく7種類に分けられる業務用3Dプリンターの造形方式について解説していきます。
材料押出法 / MEX(Material Extrusion)
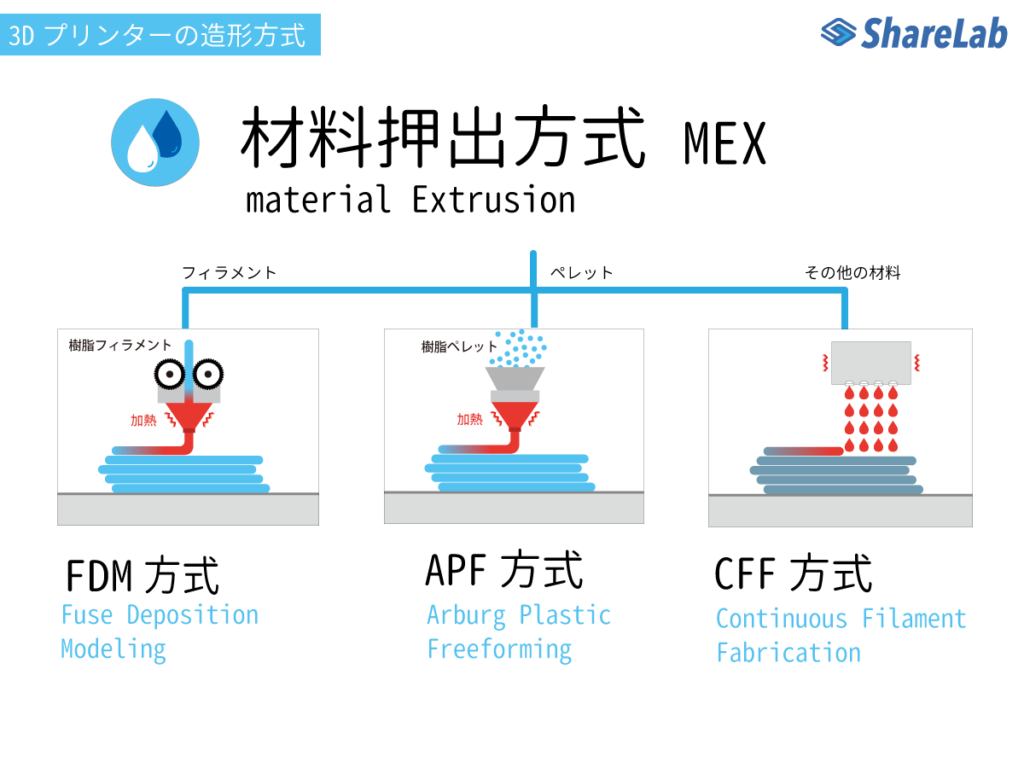
材料押出法は熱溶解積層法ともよばれます。加熱、溶融させた熱可塑性樹脂をノズルから押し出し、最終的な造形物の断面を1層ずつ固化させながら積み上げていくことで、3Dモデルデータを造形していく方式です。現在の3Dプリンターでもっとも多く使われている造形方式ということができるでしょう。
熱可塑性樹脂を用いた加工法には量産性に優れた射出成形などがありますが、金型が必要なため試作品や少ロットの生産にはあまり向いていません。その点材料押出法の3Dプリンターであれば、金型が不要であり、射出成形に似た材料を用いるため、同様の性能を持った試作品や少量の製品を低コストで製作できます。
MEX方式について
概要 | ・材料を、熱で溶融させながら造形を行う方式。 |
メリット | ・金型不要。 ・材料の管理が容易。 ・材料が豊富。 |
デメリット | ・積層痕があるため後加工が必要。 ・部品は異方性を持つため積層方向の強度が低い。 |
備考 | ・水溶性サポート材の登場でサポート除去の手間が大きく軽減できる機種が増えてきた。 ・スーパーエンプラ対応の機種も存在。 |
PLA樹脂やABS樹脂ベースのフィラメント材料などをはじめとして、さまざまな物性の樹脂に幅広く対応しています。
材料に添加物を混ぜることで、性能を向上させる取り組みも行われており、ナイロン樹脂にガラスファイバーやカーボンファイバーを混錬し造形後に後処理を行うとアルミ同等の強度を実現する取り組みなども行われています。同じように金属粉末やセラミックス粉末を混錬させたフィラメントを脱脂・焼結させることで、金属部品やセラミックス部品を造形できるとするメーカーも登場しています。
材料押出法には、使用する材料の状態や補強材の有無、造形時の設備の動き方などによって対応している設備や造形物の特徴が異なるため、用途に応じて適切な手法を選択する必要があります。
手法:FDM、APF、CFF、PEM
>> 詳細ページはこちら
材料噴射法 / MJT(Material Jetting)
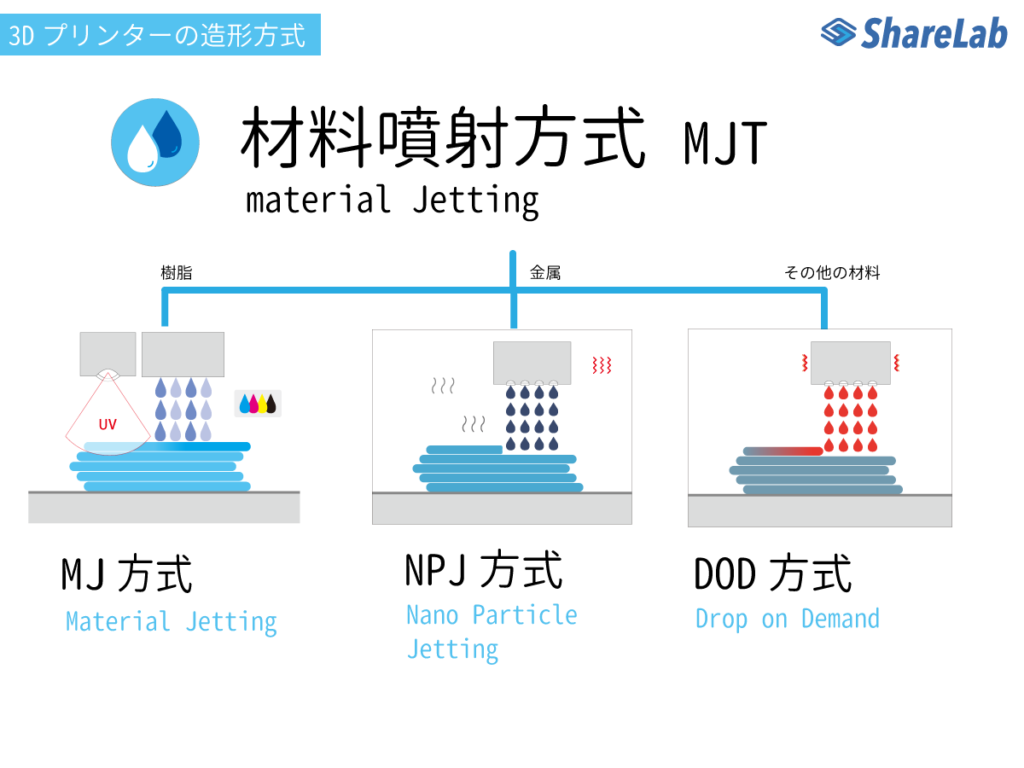
材料噴射法とは、3Dプリンターの造形方式の中でも、結合剤噴射法とともにインクジェット方式に分類されます。光硬化性樹脂や金属、シリコンなど、幅広い材料に対応している点は特徴的です。ノズルからモデル材とサポート材をステージに噴射し、材料に応じて硬化させるための紫外線の照射や加熱、冷却などの処理を加えることでモデリングします。1層ごとの厚みを薄く造形できるため、複雑な造形物でも高解像度・高精度に実現できる造形方式です。
概要 | ・インク状の液体材料を噴射しながら造形を行う方式。 ・硬化には加熱・冷却・UV光などを用いるが装置ごとに異なる。 |
メリット | ・様々な材料に対応(フルカラー、透明など) ・モデル造形用材料とサポート材の使い分けが可能。 ・精密微細な造形が可能。 |
デメリット | ・強度のある部品の造形には向かない。 ・造形速度は速くできない傾向がある。 ・材料が装置外に漏れやすく、強い薬品臭がある。空調設備が必要。 ・造形後に洗浄が必要。 |
備考 | 国内ではミマキエンジニアリング社などが製造 |
材料噴射法は、インクとなる材料にさまざまな添加物を加えることができるため、目的に応じて色や物性をコントロールできます。また、高解像度・高精度という特徴から、複雑な3D形状のデザインモデルやキャラクターのフィギュアなどに使用されることがあります。具体的な手法は、使用する材料や材料を噴射するノズルの違いによって分類されているため、使用目的に合わせた手法を選択するといいでしょう。
手法:MJ、NPJ、DOD
>> 詳細ページはこちら
粉末床溶融結合法 / PBF(Power Bed Fusion)
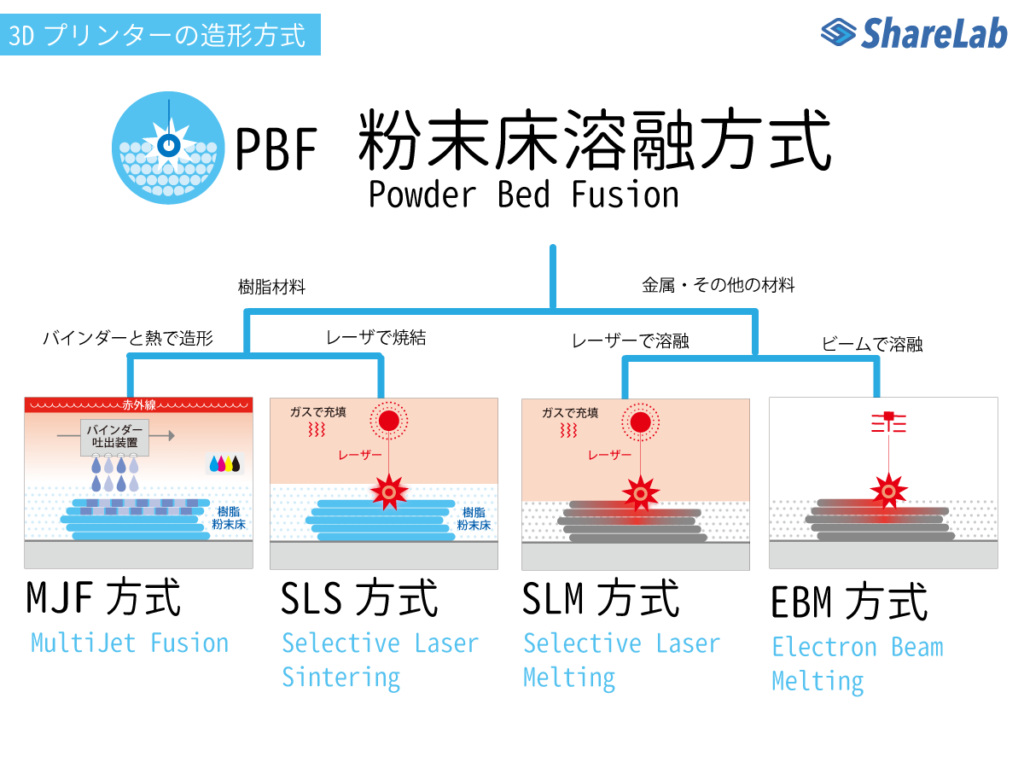
粉末床溶融結合法とは、粉末状の樹脂や金属が敷き詰められたプールの指定された部分にレーザービームや電子ビームを照射することで、モデルの断面部分を1層ずつ焼結、造形していく方式です。モデル部とサポート部は同じ材料ですが、焼結された部分がモデル部、未硬化の粉末部分がサポート部となります。
概要 | 粉末材料をレーザーなどの熱源で溶融しながら造形を行う方式。 粉塵爆発や健康被害のリスクがある粉末材料の管理に注意を払う必要がある。 |
メリット | 強度に優れる。 異方性がない。 |
デメリット | 粉末のざらつきが残るなど、表面性には劣るため、後処理が必要。 造形速度に劣る傾向にある。 粉体材料の管理が必要(防塵防爆設備、不活性ガス) |
備考 | FormlabsのFuse1のように粉塵爆発対策を施した独自材料を利用する装置も存在する。 |
モデル部とサポート部が同一材料のため、複数の材料を用意する必要がなくコストメリットがありますが、高精度を実現するためには造形時間が長くかかり、不要部分へのサンドブラストや強度確保のための含侵処理など、後処理が必要になる場合もあります。
粉末床溶融結合法の中でも、材料に樹脂を使用する場合と金属を使用する場合では、具体的な手法が異なります。また扱う材料によって加熱する際に使用するエネルギーによって分類され、融点が高い材料への適用や金属の酸化を防止するなど、特徴が大きく異なります。導入する設備規模が大きくなる可能性があるため、事前にそれぞれの手法について確認し、用途に合った手法を選択しましょう。
手法:MJF、SLS、SLM、EBM
>> 詳細ページはこちら
液槽光重合 / VPP(Vat Photopolymerization)
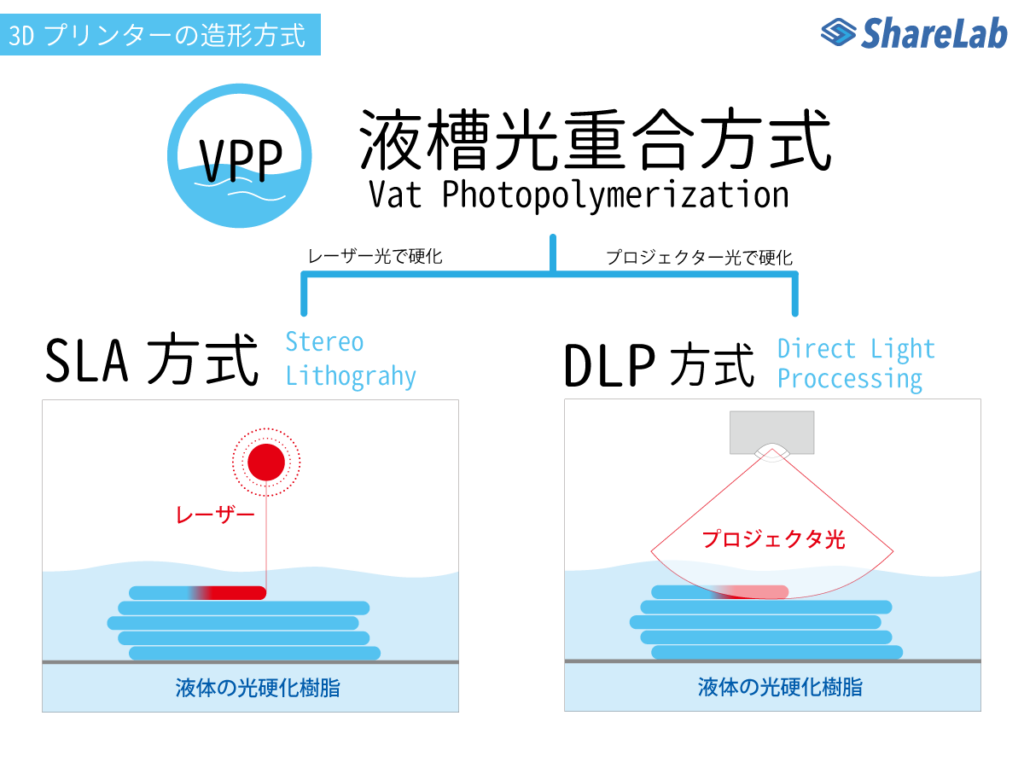
液槽光重合は光造形方式ともよばれ、タンクに貯めた液体状の光硬化性樹脂に、材料に合わせたレーザーや紫外線などを照射することで必要な部分を硬化し、積層させていく造形方式です。光硬化性樹脂が用いられますが、光硬化性樹脂は強い直射日光に弱く、耐久性が低いなどの特徴があります。そこで、主に耐久性などを必要としないデザイン用の造形物に用いられています。
概要 | ・光硬化性の液体樹脂を充填した液槽にUV光を照射し造形する方式 |
メリット | ・表面性に優れる |
デメリット | ・造形後に洗浄が必要 ・耐候性に劣る。 ・異方性がある。 ・造形に用いるモデル材とサポート材は同じ材料を利用。 ・光硬化性液体樹脂、洗浄溶液の取り扱いに注意が必要。 |
備考 | ・Carbonの3Dプリンターのように二次硬化でUV光や熱処理を加えることで 強度を向上させる材料を備えた装置もある。 ・光硬化性の液体樹脂に金属やセラミックスを混錬させ、造形後に脱脂・焼成 することで金属・セラミックス部品の造形が可能 |
液槽光重合では、光の当てる向きで規制液面法と自由液面法に分けられますが、造形時間が短い規制液面法が一般的です。また、光を照射する方法(レーザー / プロジェクター)の違いでも複数の手法に分類されています。これらの違いによって、実現可能な造形物の精度や造形に必要な時間、造形を行うために導入する必要がある設備の価格に違いがあるため、無駄な費用をかけないよう それぞれの特徴を確認することが重要です。
手法:MJF、SLA、DLP 、LCD
>> 詳細ページはこちら
結合剤噴射 / BJT(Binder Jetting)
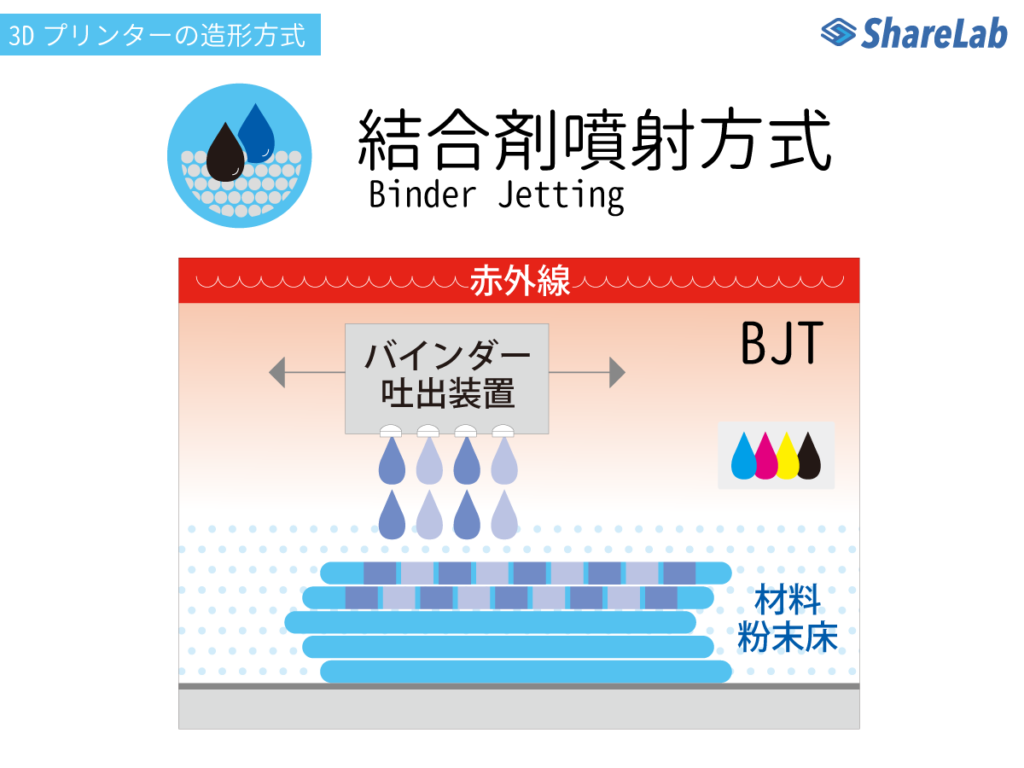
結合剤噴射は、材料噴射と同様にインクジェット技術を用いた造形方式です。粉末状のモデル材を敷き詰め、造形したい部分に対して、バインダーとよばれる結合剤をインクジェットノズルから噴射し、熱反応や化学反応を利用して固めます。モデル材に使用できる材料は幅広く、樹脂や金属、砂や石膏が用いられます。
モデル材とサポート材が同一であり、材料を硬化させる際に用いる付帯設備が不要な点で、コストを削減できる可能性があります。一方で、モデル材には結合剤が含まれているため、用途によっては強度が不足する点がデメリットとなります。強度が足りない場合には、樹脂材料の場合には含侵処理、金属材料の場合には焼結処理により結合剤を燃焼させるなどの後処理が必要です。
概要 | ・バインダー(結合剤)を材料粉末に照射しながら造形を行う方式。 ・インクジェット方式の一つ。 |
メリット | ・造形速度が速く、生産性が高い。 |
デメリット | ・強度に劣る傾向にある。 ・微細な造形が不得手な傾向がある。 |
備考 | ・HP社のMJF方式は、光硬化と熱硬化を併用して強度、精密性を向上させている。 ・デスクトップメタル社のShopシリーズは、バインダージェット方式で造形後、脱脂焼成を行うことで、金属部品を造形する。 |
樹脂や金属以外の石膏や砂を用いる場合は、金型などの製作に用いられており、通常の金型製作に比べて制作時間やコストを低減できます。このようにさまざまな材料を用いることが可能な結合剤噴射ですが、素材が金属か金属以外で造形方式が異なるため、それぞれのを理解して手法を選択する必要があります。
手法:BJ
>> 詳細ページはこちら
指向性エネルギー堆積 / DED(Direct Energy Deposition)
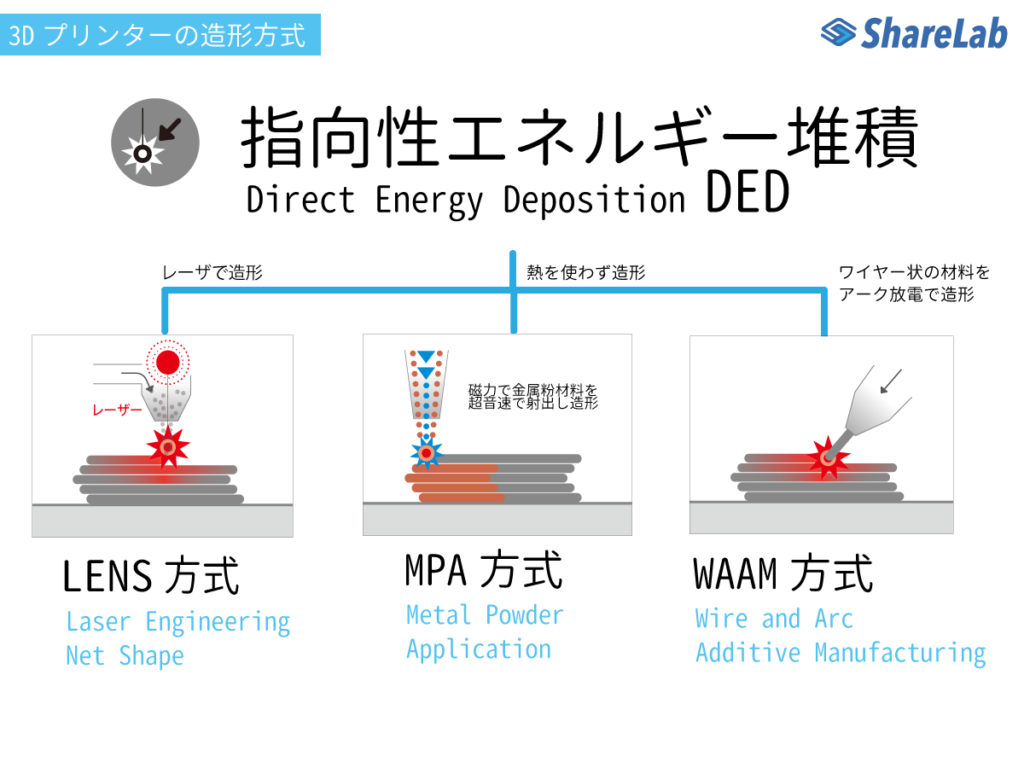
指向性エネルギー堆積法は、レーザー(メタル)デポジションとよばれることもあり、粉末状やフィラメント状の金属をノズルから排出しながら、レーザーや電子ビームなどで加熱、溶融し、積層する造形方式です。粉末床溶融結合法の発展版とも言われます。
概要 | ・熱などの指向性のエネルギーで材料を溶融させながら造形を行う方式。 ・粉末材料以外にも、溶接用ワイヤーを利用する方式もある。 |
メリット | ・原理上、大型化が容易。 ・造形が早い(生産性が高い) |
デメリット | ・微細な造形が不得手 |
備考 | ・国産DEDは装置として三菱電機、ニコン、日本電産マシンツールズなどが製品をラインナップ。 |
材料は、粉末状になっていれば複数のものを組み合わせることができるため、モデルの活用目的に応じた特性を実現できる可能性があります。また、金属3Dプリンターの他の方式に比べると造形速度は速く、造形時間を短縮できるのは大きなメリットです。
指向性エネルギー堆積法の中でも、材料を溶融する際の指向性エネルギーに何が使われるかによって手法が分類されます。中には、圧縮したガスにより噴射する金属粉末の速度を高めることで、材料がぶつかる際のエネルギーで結合させる手法もあります。
材料の状態や金属を溶融、結合する方式により複数の手法に分類されています。選択する手法により準備すべき組織などが大きく異なるため、確実に確認しましょう。
手法:LENS、MPA、WAAM
>> 詳細ページはこちら
シート積層 / SHL(Sheet Lamination)
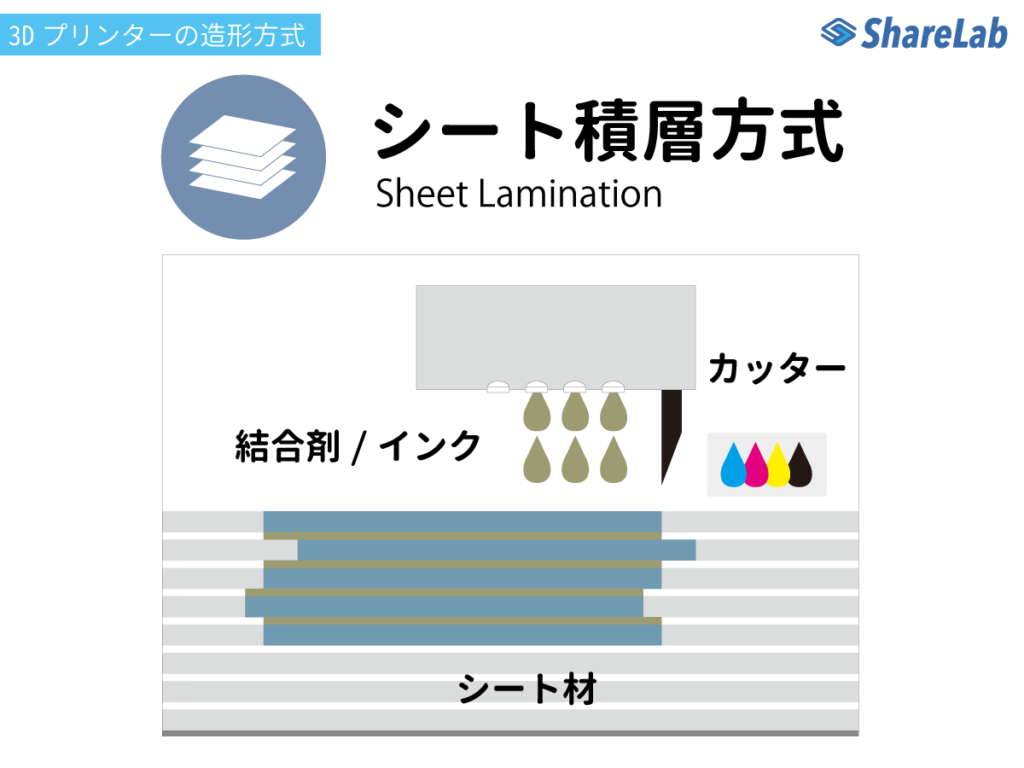
シート積層法はラミネート積層法ともよばれ、紙や樹脂、金属などの薄いシート状の材料を、1層ずつその層の断面形状に合わせた輪郭線で切断し、設計した形状になるまで接合、積層を繰り返す造形方式です。材料を硬化させる際に加熱や紫外線の照射など、化学反応を起こす過程が不要な場合が多く、他の造形方式に比べると設備の構成を簡素にすることが可能です。
シート状であればさまざまな材料に対応することが可能であり、接着をする際には材料に合わせて特殊な接着剤や超音波照射が用いられています。紙や安価な樹脂などを用いることができるため、物性にこだわらなければ、他の造形方式に比べて安価にデザインモデルを製造できます。
また、もし造形物の物性が必要な場合には、必要な物性を実現できる材料を用いたり、積層させるシートの間に補強材などを挟みこんだりすることで、実現可能となります。
シート積層法では、各層を接着する方法の違いによって使用できる材料や造形方式の特徴が異なるため、目的を明確にし、それを確実に実現できる設備の導入を検討しましょう。
手法:SDL / LOM
>> 詳細ページはこちら
3Dプリンターの造形方式は目的に合わせた選択が重要
3Dプリンターのさまざまな造形方式7種類について、それぞれの特徴を簡単に紹介しました。それぞれ適用できる材料や造形できるモデルのデザイン、造形時間や設備・造形コストなどに大きな違いがあり、すべてに対応できるような3Dプリンターは存在しません。
3Dプリンターを導入する目的を再度明確にし、その目的を実現できる造形方式、手法を選択できるように、さまざまな調査が必要です。この記事で紹介した造形方式について、より詳しい情報が必要な場合には、それぞれの造形方式を詳しく解説したページへのリンクを各項目ごとに設置してありますので、そちらの内容をご確認ください。