世界最大手の3Dプリンターメーカーであるストラタシスはフィラメント材料を使ったFDM方式に強みを持つ3Dプリンターメーカーだ。技術力に秀でたAM業界各社をM&Aしながら、3Dプリンターでのモノづくりをリードし、いまでは売り上げの半分が最終部品関連となるに至ったという。
AM業界をけん引してきたストラタシスだが、コロナ禍を挟んでどのような装置、材料、事例にアップデートがあったのか。DMM.comの3Dプリント事業部の元事業部長で、現在は3DCGと3DCADをつなぐアプリ開発に取り組む株式会社ツクリテの代表を務める川岸 孝輔 氏が、当時付き合いのあったメーカー各社に連続取材していく。今回はイスラエルに本社を置く、ストラタシス社の日本法人、株式会社ストラタシス・ジャパンにお話を伺った。
( 語り手:株式会社ストラタシス・ジャパン 竹内 翔一 氏、聞き手:川岸 孝輔 氏、編集:シェアラボ編集部 伊藤 正敏 )
目次
ストラタシスの事業拡大について
川岸氏:ここ2年間の3Dプリンターの装置・材料のアップデート情報と、最終製品利用の最新状況を伺いたいと思っています。また、海外では活用が進んでいる状況がある中で、日本ではまだ実例が少ない理由もストラタシスさん独自の視点で伺えればと思います。それと御社は3Dプリンター企業をどんどん買収して大きくなってきている会社かなと考えておりますので、そのあたりも可能な範囲でお聞かせいただければと思います。
竹内氏:3Dプリンターの市場が、年率で2桁成長を期待されている中、特に樹脂マーケットは引き続き成長を続けていくと考えています。樹脂マーケットは2025年までに3Dプリンター市場全体の60%までに成長することを期待しています。そのような中、以前のストラタシスはPolyJet方式(インクジェット方式)とFDM方式の2つの系統しか持っていませんでした。その2つでカバーできる樹脂マーケットは約30%しかなく、これでは不十分だということで、数年前から新しい技術を持った会社の買収を推進しました。現在では光造形方式(SLA方式とDLP方式)や粉末樹脂造形(PBF方式)もカバーできるラインナップとなっています。
PolyJetの最新アップデート ― ファブリックに対応
竹内氏:PolyJet方式は試作品の製造に向いている表現力の高い造形方式ですが、最近特に力を入れているのはファブリック領域です。インクジェット方式のPolyJetで素材に対して直接プリントして造形し、積層をしていくソリューションを今展開しています。
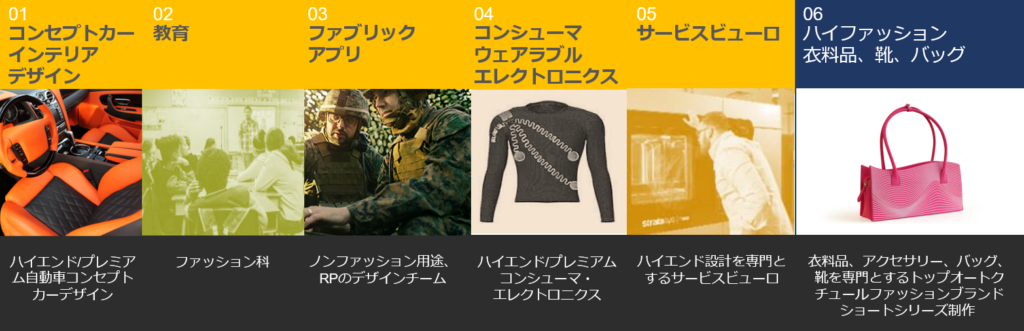
硬質のものやメッシュ形状のものにもプリントできますので、服だけではなく、車のインテリアなどにも活用できるのではないかと考えて展開しています。
川岸氏:それは平面のUVプリンターのように印刷したものを貼り込んでるということでしょうか。
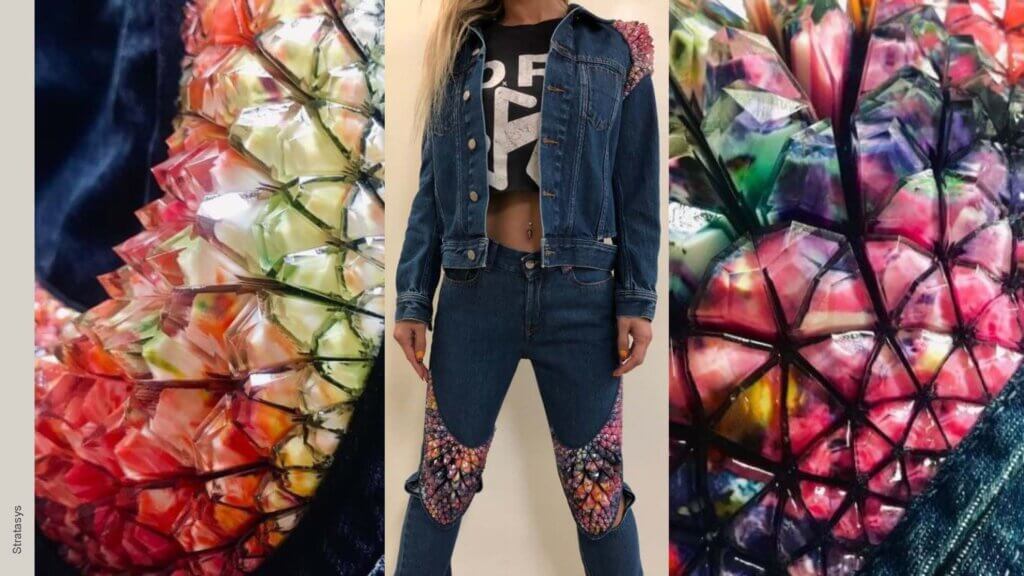
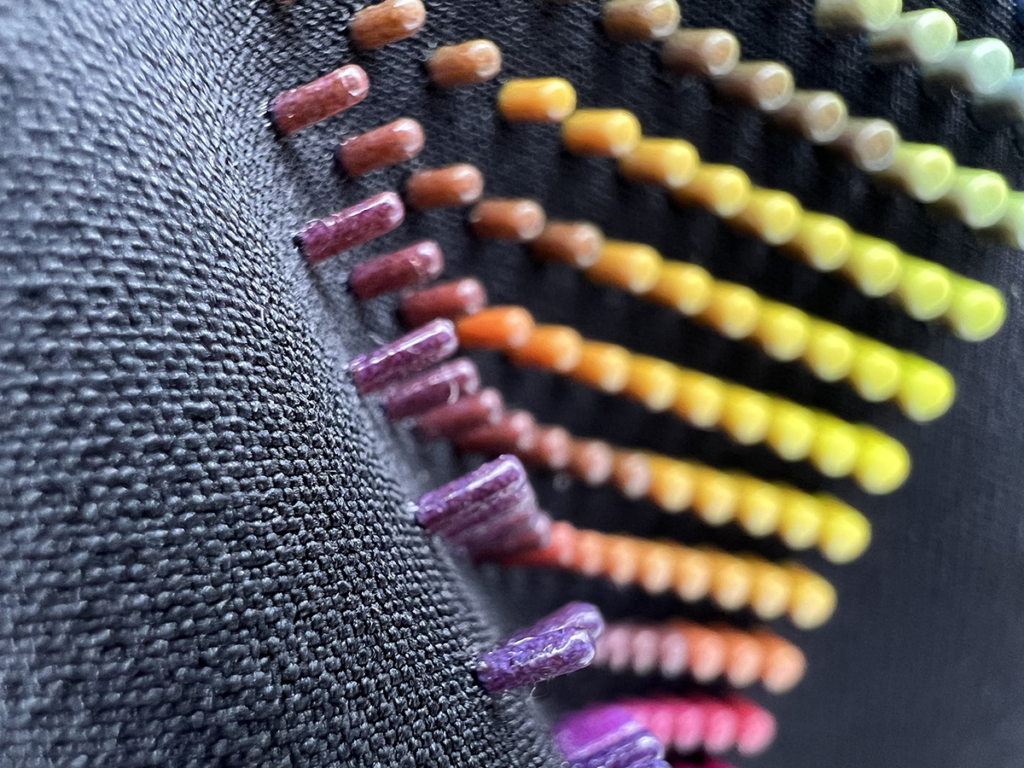
ストラタシス:そうです。既存のUVプリンターだと高さが1mm未満しか出せないのですが、弊社のものだと高さがある程度出せるので、本当に立体的な造形物も表現できます。特に皮やスエード、綿などへの密着性も高く、洗濯してもはがれないようにプリントできます。
川岸氏:すごくイノベーティブというか、今までできなかったことですよね!デザインの点で新しいことができそうな、インスピレーションが湧きそうな内容で面白いです!
ストラタシス:そうですね。実際に引き合いは多く、今までコンタクトがなかった方々、特にファッション業界の方々にものすごく興味を持ってお問合せいただいていますね。
国内製造業へのフルカラー3Dプリンターのアプローチ
竹内氏:国内メーカーの製造業の方はフルカラーの3Dプリンターを宣伝しても「カラーはいらないよ」という方もいらっしゃるので、フルカラーモデルの「J55 Prime」のプラットフォームですが、モノクロの機種を価格を落として2023年に販売開始しています。カラーにはもちろん今後もフォーカスはしていくのですけど、エンジニアリング事情に沿った機能を持ったPolyJetも引き続き提案していくつもりです。
FDM方式3Dプリンターの大型化で需要をキャッチ
竹内氏:現在プロモーションしているのが、FDMのさらなる大型化です。以前からあるNylon 12CFやABS-CF10、これに加えてNylon-CF10という材料が新たに使用可能になった「F190CR」「 F370CR」という装置で利用できるようになりました。
炭素繊維材料は今までマークフォージドさんがかなり強かった分野なのですが「もう少し大きな造形サイズに対応できる装置はないのか」というお客様のご要望があり、「F190CR」「F370CR」という装置を提案しています。大型のものを造形するために、分割造形して後で貼り合わせるのは効率が悪いので、一気に出したいというわけです。そうした声に応えて1,000mm幅を造形できる「F770」が登場しました。海外の動向を考えると国内でも、さらに大型のものを作りたいという企業が増えているのを感じます。
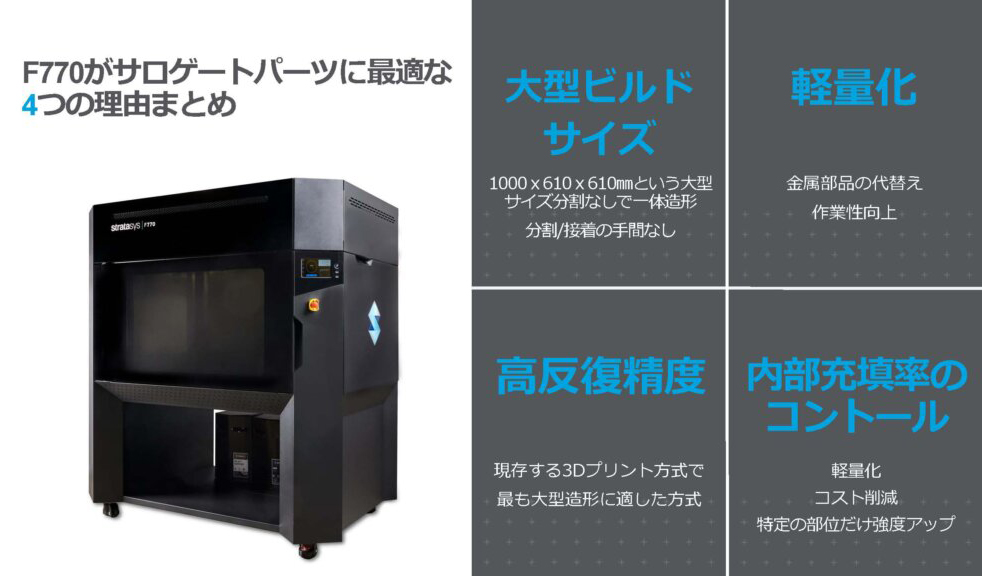
川岸氏:日本でも3Dプリンターを使った商品開発・製品開発をする企業が出始めている点は、とてもよいトレンドですね。
製品開発に3Dプリンター活用を提案
竹内氏:弊社では製品開発分野での3Dプリンター活用を提案しています。しかしこれまではFDM方式の3Dプリンターが7,000~8,000万円ぐらいすることから難しかったんです。それが今では大型の造形が可能なものでも素材を絞ることで価格を大分下げることができ、提案のハードルが下がってきました。
CADが使えるエンジニアは限られていて、現場の人だと見方が分からない、感覚がつかめないという状況があります。それを3Dプリンターで現実世界に落とすことで、いろんな人が簡単にアクセスできます。またそれをデジタル空間にフィードバックして設計してといった循環をすることで開発期間を短くできるんじゃないか、という提案をしています。こうした開発段階の部品製作のことを海外ではサロゲートパーツと呼ぶことが多いようです。
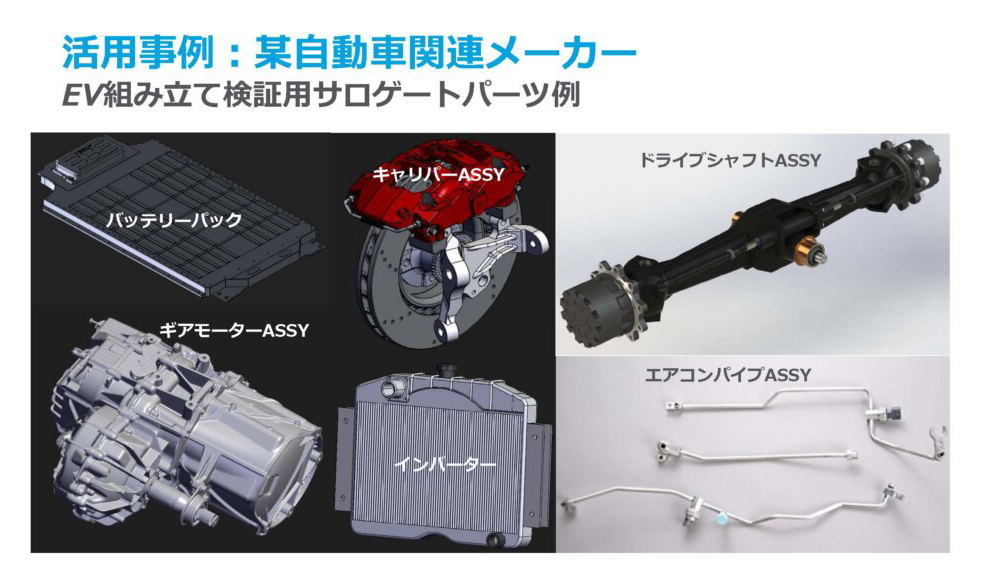
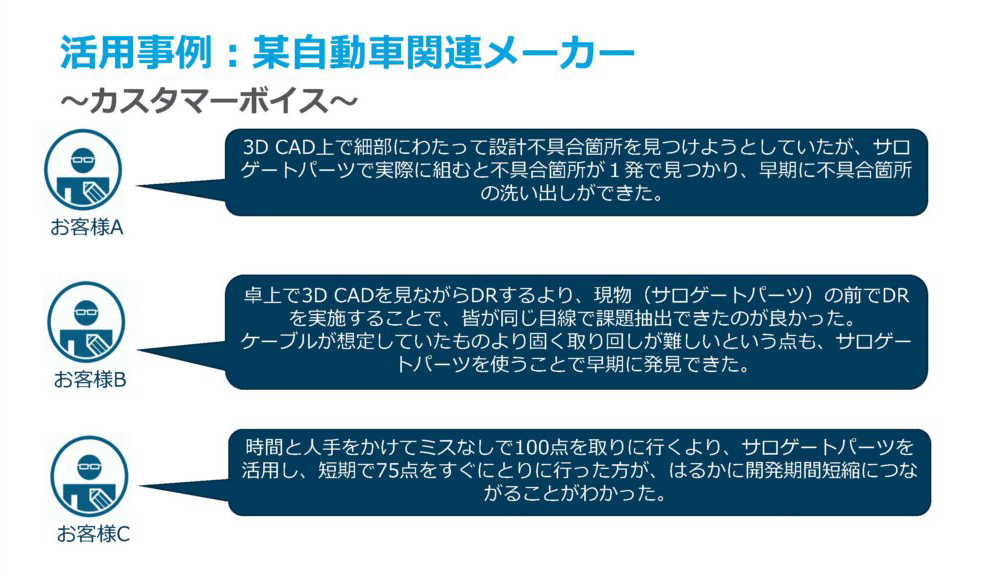
川岸氏:3Dプリンターを活用すれば、開発開始初期から生産技術だったりとか巻き込んでやれるので、いままでの開発と全然違う 発想になってくると思います。すごく面白いです。
日本と海外の3Dプリンター活用への考え方の違い
川岸氏:ストラタシスさんも守秘義務で話せないと思うのですが、公開されていないだけで、どんどん3Dプリンターを使っている会社さんって増えているんじゃないかと思っています。ですが重要なのは採用実績よりもマインドの方がと思うんですよね。「こういう風に考えた結果、3Dプリンターを使った」という話を拡散した方が、多くの企業が追随して、最終的に使われる傾向が強まるんじゃないかと思っているんですが、そのへんはいかがですか?
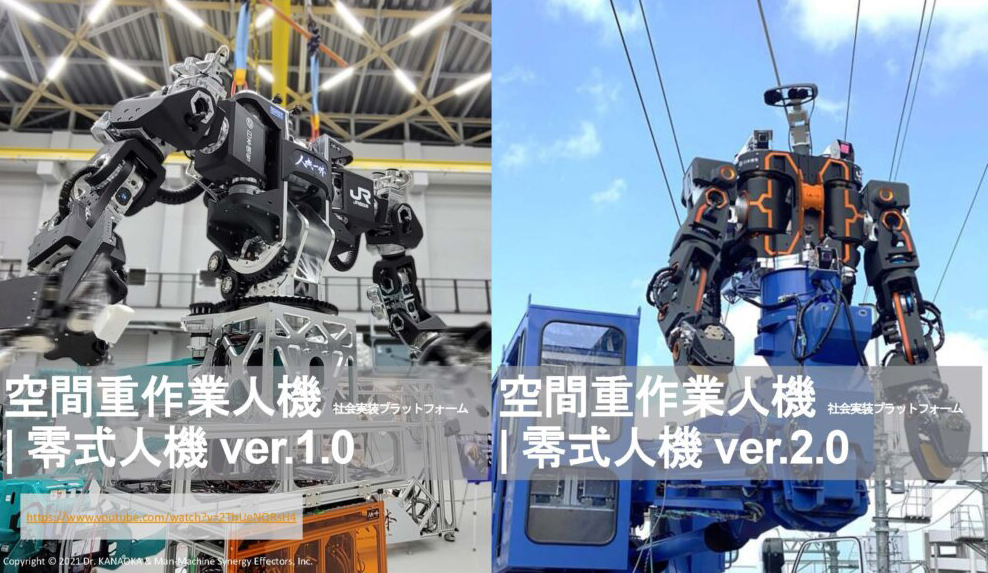
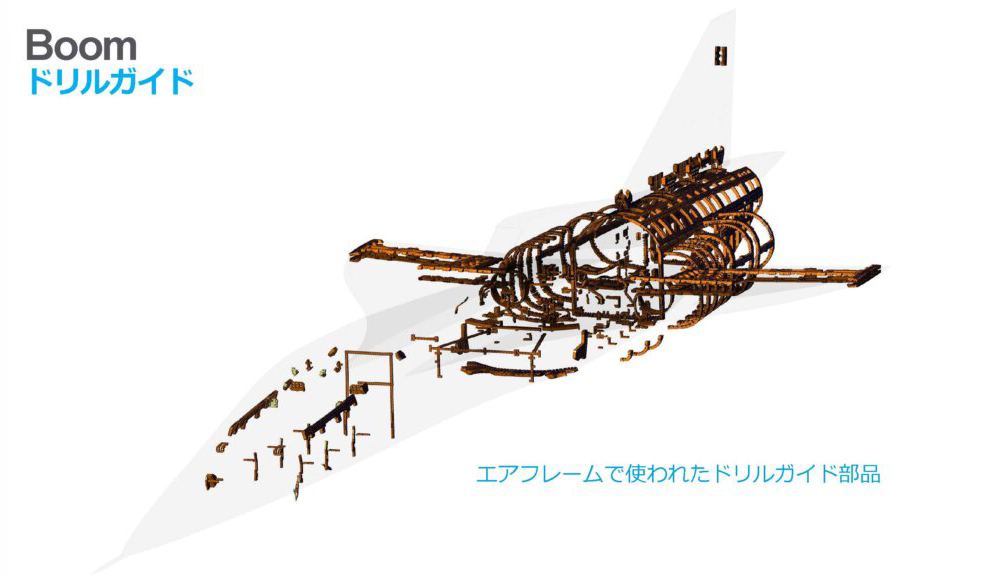
竹内氏:おっしゃる通りですね。今3Dプリンターが使われている事例は、結局アディティブ・マニュファクチュアリングであることで「すごく差別化ができて優位性が保てるがゆえに使った」「今のモノづくりではできないので3Dプリンターを選んだ」といった話です。「3Dプリンターを使う必然性」が求められています。
一方で海外での使い方は「必然性ではなく最適化」なんです。これまでの工法も3Dプリントも選べる中から、最適な工法を選んでいるんですね。日本ではデザインのサイクルを短くしなくちゃいけないときに必然性が生じて3Dプリンターを選んでいますが、十分な時間がとれる場合、選ばなかったかもしれない。ここが大きく考え方が異なるところです。
日本では「必然性に迫られて3Dプリンターを選択している」という背景があるからこそ、事例を公開することが製品の弱点や技術力の限界を示してしまうのかもしれません。だから事例公開に躊躇してしまうという面が少しあるのかなと感じます。
川岸氏:なるほど、その考えは頭になかったです!日本では必要性に迫られて使われ、海外では最適化を目指して活用されている。日本でも最適化目的で使われている事例があるなら、積極的に公開してほしいですね。
竹内氏:本来であれば「カイゼン」っていう取り組みは日本が最も得意とするところであって、たとえばサプライチェーンの分断やリスク回避、需要変動の全体最適を考えたらアディティブ・マニュファクチュアリングを選ばない理由がないぐらいなんですよ。ただ、その部分は置いておかれていて、なぜか違うところだけ最適化を図ってきてしまってます。だから新しい工法が少し浸透しにくいのかもしれません。
取材後記
ストラタシスの竹内氏の「もう海外では3Dプリンターを特別視していないので、最適化の観点からフラットに選んでいる」という指摘はなるほど、と肚落ちできるものだった。日本の製造業を見渡すと、今はその前夜で、試作のための工法、既存工法以外に差別化要素としてAMにも取り組むといった姿勢が主流のように見受けられる。3Dプリンター活用が定着した際には、日本の製造業の中でも、同じようなフラットな感覚でAMを選択できる姿が一般的になっていくのかもしれない。
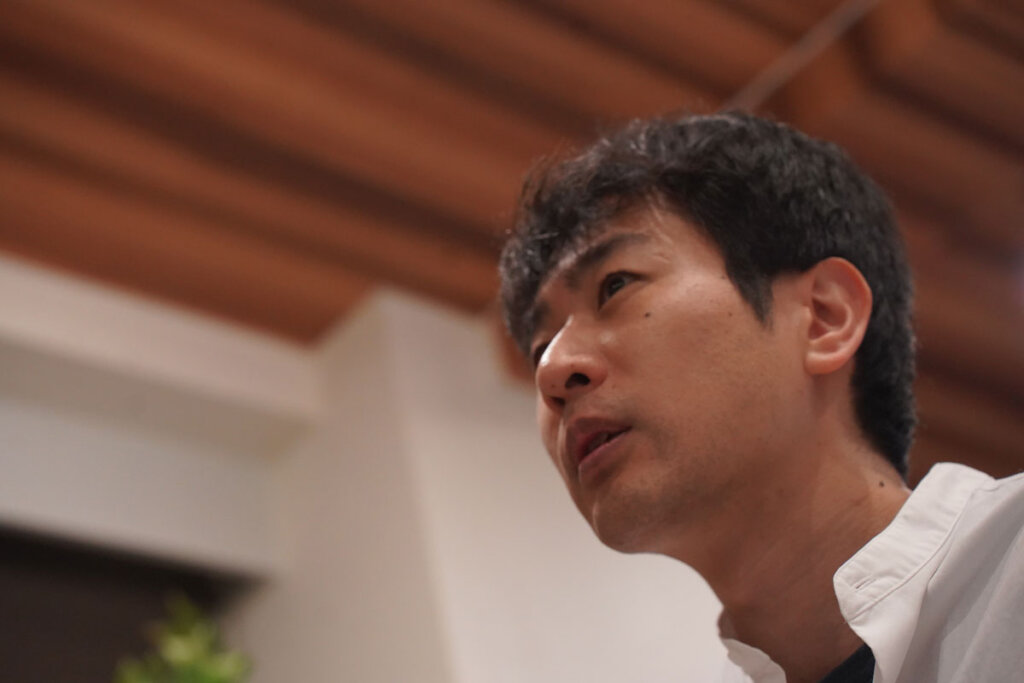
【インタビュアー】
川岸孝輔(かわぎし こうすけ)
楽器メーカーで製品企画から製造まで幅広く経験後、大手インターネット関連企業でオンライン受託造形サービスを統括。日本最大規模のサービスに育てる。現在は独立して株式会社ツクリテを設立し、製造関連のデータ製作だけでなくデジタルツインを実現するMRアプリ開発を行う。「楽しみながら新しいことを学び続ける」ことをモットーにしている。
コーポレートサイト:https://www.tkrite.com/
note:https://note.com/tkrite/