日本AM協会は2024年5月15日に「2024年度第1回正会員会議」と「第1回総会」をDMG森精機(東京グローバルソリューションセンタ)にて開催した。来場49名、オンライン30名の合計79名様が参加。またAM交流会では経済産業省、日産自動車、豊田自動織機、マツダ、デンソー、いすゞ自動車が参加し、懇親会では参加者間で活発な意見交換がされた。(上部画像は日本AM協会 2024年度総会)
日本AM協会ウェブサイトにて当日のプログラム、動画を公開した。
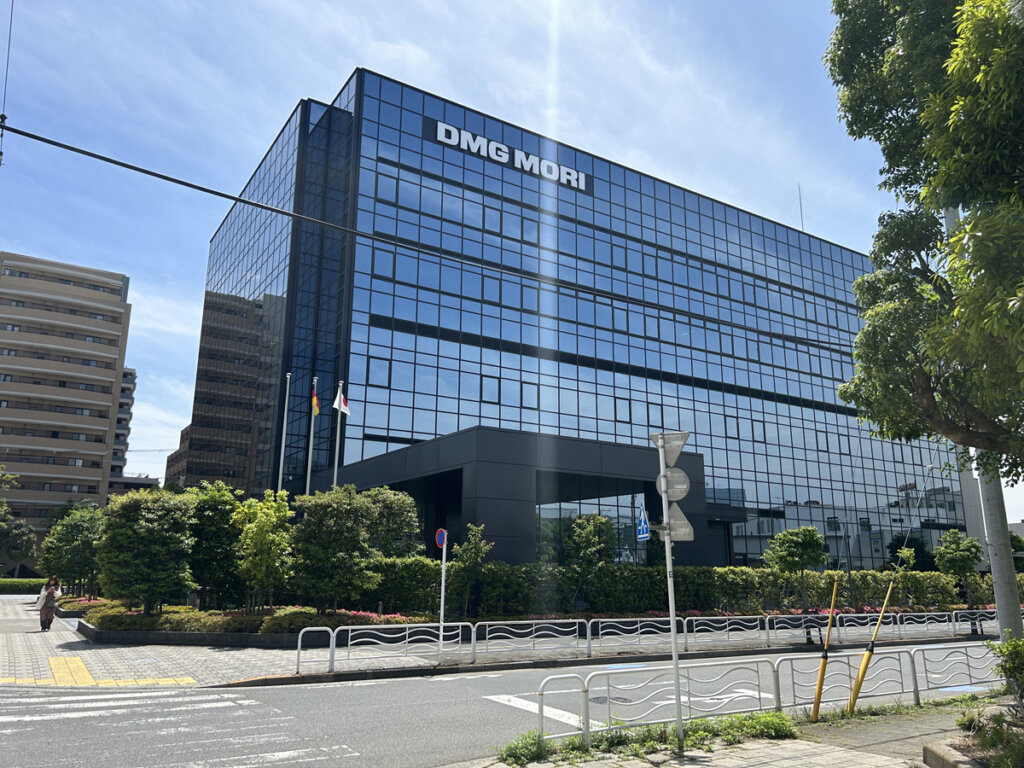
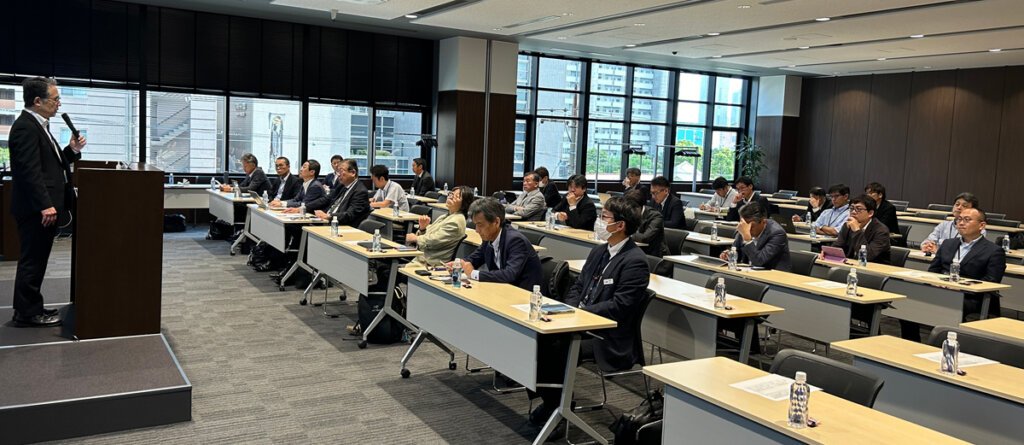
賛助会員としてイントリックス株式会社 ShareLab事業部 丸岡が参加し、AM交流会での参加発表者の要点を寄稿したので、掲載文を以下に引用する。
目次
AM交流会での参加発表者の要点
全体
日本ではAM活用が世界的に広がる防衛軍需、航空宇宙、医療などの産業規模が小さくAM産業は先進地域の規模には達していない。主軸の自動車産業ではこれまでAM活用、普及は試作関連に留まり、製品部品生産に進展しなかった。その背景には、①自動車部品は他の機械部品と比較して極めて安いコストで製造されていること、②市販車部品としての性能品質、耐久性要求が高い一方で現状のAM製品、材料、技術で満たすにはギャップが大きいことがあった。
しかし、近年の世界的な社会経済環境の変化により、日本の自動車産業の国際競争力低下、衰退の危機感が広まりつつあることから、特に製造に関する課題解決にAMを使う需要が高まってきた。
以前より各社でAMの基礎評価研究をしてきた上で、実際の活用に取り組み始め、要求に対するAM能力・技術の限界が明らかになった。自社での解決が難しいと感じる担当者が会社の垣根を超えた協働を模索し始めている。
実際に、自社だけでなく、供給者、競合他社含む需要者含め、実際何を求めているのか、何が必要なのかを具体的に公表し、協働を指向する企業が同時複数現れてきた。また自動車以外の重工業、航空宇宙産業や自社新規製品やビジネス開発を狙う中小企業にも同様の動きが見られるようになった。こうした傾向はこれまでになかった変化である。 昨今は既存または新規のAM産業関連普及・研究団体組織への企業参加の増加や共同研究プロジェクト、宣伝啓蒙活動の活発化がみられるが、需要者の課題感の共有と協働での解決を求める動きが背景にあることが垣間見えた機会であった。
自動車OEM・サプライヤーのAM活用の現状と見通し
自動車大手OEM・サプライヤーでは2016年前後から、製品部品生産を想定した、特に金属AMの品質、信頼性、コストダウンなどの検証と基盤技術研究開発が取り組まれてきた。同時に社内試作部門で生産部門含めた社内周知や需要に応える設備や技術の積み上げを各社独自で行ってきたが、下記の認識と課題感がある。交流会での発言要旨をダイジェストでお届けしたい。
- 社内のAMに対する認知や必要性はようやく高まってきた。一方で、多くの社員は展示会などにも行けず、現物を見る機会も少ない。詳しい人も各部署に散在していて、AMを推進する人も「知っている人」や「味方」を社内で探すのに苦労しているのが現状だ。そこで、社外から情報収集したり、協力者を作ったりするほうが時間と工数で有利と認識し、実際に行動しはじめている。実際、金型の最適冷却化などで先行している企業と学会などで交流を行い、同様の活用研究を始めた例も出てきた。
- AMの製造活用の大きな障害の一つは、AMでできる可能性のある製品部品の機能性の「絵が描けない」こと。わからない新しい技術に対して、既存技術に詳しい人ほど否定する傾向があるが、否定は知識経験がない人でもできる。正攻法はできることをひとつずつ証明することだが、時間がかかりすぎる点が問題だ。これまでのできていなかったが、欲しい機能から逆にユーザーサイドが明確なニーズを示し、AM装置メーカーに対して、モチベーションを示すことが大事と考えるようになった。
- これまで一般にAMの利点とされるDfAM設計や複数部品一体化も試したが、成功していない。最大の理由はコストだ。自動車部品は極めて安いコストでできていて、多く、安く、何回造っても同じものができるようにしないとAMは導入できないという認識に至る。一方、目標値を(提供サイドに)発信したり、「こうして欲しい」といった具体的な要望や社内導入のための方法論も提供してこなかった反省もある。世界で一番安いAM部品を作りたいと考えている。
- お客様から古い車の交換部品の要求があり、メーカーとしては応えたく社内・サプライヤーに金型の保管を頼っているが、増え続ける金型の管理に苦慮している状況が続いている。「金型を捨てること」がゴールではなく、「作り続けるにはどうするか」が重要だが、既存工法での少量生産は効率的ではない。まず製造領域から鋳造砂型AMの活用検討を始めるなど取り組みを行い、単純置き換えだけでなく新たな付加価値がプラスできることが分かってきた。生産全体の中でAM効果を最大限引き出そうと考えている。またその活動は共有できればと考えている。今後AM技術を最大限利用したモノづくりに向けては1社ではできないと認識したが、社外との接点が少なかったので、自ら社外企業に多数出向き情報収集と協働を進めている。
自動車部品製造に金属AMを使う上で、既存製造技術ではコストが高い加工をAMで改善できることが重要。主に求める材料はアルミ系だ。鉄やシリコン合金で伸びがない材料で、鉄系としてステンレスはあまり需要がない。AMで難しいとされるハイカーボン材料が必要。
海外自動車メーカーのAM活用事例はアルミ系が中心で高額車はチタン系が使われる。動的強度を要求しないエンブレムなどには使える。今後見込まれる需要はEVの熱マネジメント系の需要で、ここにAMを使ってくるのではと見ている。
日本AM協会の関連記事
今回の記事にに関連するものとして、これまでShareLab NEWSが発表してきた記事の中から2つピックアップして紹介する。ぜひあわせてご覧いただきたい。
設計者からAMソフトウエア・装置販売ビジネスに20年以上携わった経験と人脈を基に、AMに関わるみなさんに役立つ情報とつながりをお届けしていきます。