オランダの装置メーカーであるHuisman Equipment(以下、ハウスマン)は、独立した認証機関であるロイド・レジスターの監督のもと、3Dプリント技術を使い350トンの重さに耐えられるクレーンフックのテスト運用に成功したことを発表した。(写真はハウスマン製のクレーンフック / 出典:ハウスマン)
目次
ハウスマンの3Dプリンター活用事例
ハウスマンは、2015年以来金属3Dプリンターのワイヤー&アーク積層造形(WAAM)方式の研究開発に多くの投資を実施し、高張力鋼板を用いた中型から大型の部品を製造している。2018年にはハウスマン初の3Dプリンターでクレーンフックの製造に成功。80トンの重さまで耐えられる強度の高さもテストの結果実証された。
そして今回、約9倍もの大きさとなる約170×130cmの新たな大型ワイヤーフックの製造に成功した。重量は1,700kgで、積載量は350トンまで耐えられる強度へバージョンアップしている。各フックには、約90kmの溶接ワイヤーが使用されている。
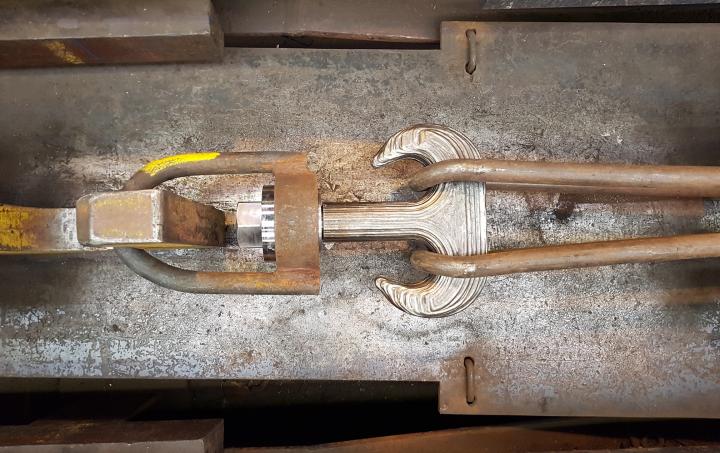
金属3Dプリンターを利用した背景
巨大な構造物を鋳造技術を用いて作る場合、内部の品質を均一にすることは難しい。従来の鋳造技術では、溶けた金属を型に流し込み、冷えて固まることで任意の形状に金属構造物を作ることができるが、製造工程中に温度変化が起こり、外びけや内びけなどの形状不良やガスによる空洞が発生することがある。作業中に高温になった金属内部を不具合がないか確認することは非常に困難で、納期が延びてしまうといった課題があった。
その課題を解決できる手段として3Dプリンターが採用された。
5年間にわたる3Dプリント製品の研究・開発・テストを経て、高品質なクレーンフックの製造に成功した。3Dプリントで製造したクリーンフックの利点を4点あげている。
- プロセスと素材の品質を高度にコントロールできる
- レイヤバイレイヤータイプの製造により、新しい形状の部品製造が可能
- 重要部品のコストとリードタイムの削減
- 同一製品の中で、強度、延性、耐摩耗性、耐腐食性などの材料特性をカスタマイズできる
採用されたワイヤー&アーク積層造形(WAAM)方式とは
金属3Dプリンターにはさまざまな造形方式がある。それぞれに特徴があり、得意不得意が存在している。パウダーヘッド方式が現在は主流となっており、多くのメーカーからこの方式の3Dプリンターがリリースされている。しかし、使用用途によっては別の方式が良いなど、種類別に特徴を押さえておくことは重要だ。そのため、今回は代表的な3つの方式について紹介する。
なお、ハウスマンのクレーンフックに採用されたWAAM方式は材料コストや造形スピードなど品質を維持したまま、大型化やコスト削減、納期短縮を可能にすることにすぐれている。
製造方式 | 特徴 | メリット | デメリット | 3Dプリンターの価格帯 |
---|---|---|---|---|
パウダーヘッド方式 | 金属粉末を敷き詰めたベッドにレーザーや電子ビームを当て必要な部分を溶かして固めていく方式。現在は主流方式となっており多くのメーカーからこの方式の3Dプリンターがリリースされている | 再現性が高く、寸法精度も良い | 造形範囲を大きくできない、造形時間がかかる | 3,000万~2億円 |
メタルデポジッション方式 | 指向性エネルギー堆積(DED)方式ともいい、溶融した金属材料を所定の場所に積層・凝固させて造形する方法 | 高速造形 レーザークラッディングで金型の補修、部品の補修などに対応可能 | パウダーベット方式より形状精度は低い | 1億~3億円 |
ワイヤー&アーク積層造形(WAAM)方式 | 溶接機器によって、連続的に溶接ワイヤとシールドガスを半自動で供給し積層していく方法。粉末は発生せず粉塵爆発等の危険もなく、比較的高速に造形が可能 | 価格も安く汎用性が高い(粉末に比べ材料費が1/10) | 製造コストが高い | 2,500万~4,000万 |
ハウスマンの今後の展望
ハウスマンは、チェコ共和国のスヴィアドノフにある生産施設のロボット作業場を拡張する計画を立てており、現在3台の溶接ロボットを保有している。生産能力を向上させることで、ハウスマンは重量5,000kgまでのクレーンフックを生産できるようになるとのこと。
3Dプリンター技術を活用した高品質・低コストのクレーンフックのさらなる進化に今後も期待したい。
関連情報
国内外の3DプリンターおよびAM(アディティブマニュファクチャリング)に関するニュースや最新事例などの情報発信を行っている日本最大級のバーティカルメディアの編集部。