2019年は造形材料メーカーの展示会での新しい展示が大幅に増えた一年だった。樹脂も耐熱性、絶縁性、導電性、生体適合性の高い樹脂が相次いで投入されたし、金属の鋼種も増えた。またセラミックスも具体的な取り組みが複数発表された。
そんな中、透明度が高いガラスが積層造形の材料として利用できるという事で非常に高い関心を集めているのが今回ご紹介する九州大学藤野研究室の石英ガラスだ。
非常に透明度が高く、耐熱性にも優れ、機械的強度も高い石英を自在に造形できる。今回のTCT Japan 2020で講演も予定されている藤野教授に石英ガラスの魅力、研究の経緯、これからの取り組みに関して伺ったのでご紹介したい。
***
――藤野先生のご活動に関して教えてください。
私は九州大学で石英ガラスの材料研究に取り組んでいます。石英ガラスは耐熱性、耐薬品性にすぐれ、光の透過率も高く、機械的な強度も高い。非常に優れた素材です。有名なツタンカーメンの胸飾りにも隕石由来の石英ガラスでできたスカラベがあしらわれていますが、3000年以上経過した今も、経年劣化することはありません。経時変化にも非常に強いのです。
私は石英ガラスこそ「ガラスの王様」だと思っていますが、優れた特性をもつがゆえに加工難易度も高く、扱っているメーカーも限られています。非常に優れているのですが非常に高価な素材といえます。そんな石英ガラスを廉価に多用途に使うことができる材料にすることがゴールです。
研究の成果として、2019年10月にプレスリリースしたのですが、石英ガラスを3Dプリンターで自由に造形できる方法を確立することができました。液体樹脂と特別に用意した石英ガラスの原料を配合して、光造形で自在に造形できる材料として開発しました。3Dプリンターで造形し、その後脱脂をして、焼結炉で焼きこみます。後加工なしで自由に造形できるようになります。
このアプローチでは、パラメーター調整等は必要ですが、液体樹脂と金属粉を混合した造形液をつかっている3Dプリンターで脱脂、焼結プロセスを経るタイプあれば、どの3Dプリンターでも利用できる石英ガラスの造形材料を提供できます。
――石英ガラスも3Dプリントできるんですね!これは日本初ですよね?
私の知る限りでは、石英ガラスを3Dプリンターで出力するという報告は研究段階で、世界で成果が出ている研究グループはほとんどありません。ヨーロッパの研究者が発表している例もありますが、造形精度などの面でまだまだこれから、という段階です。今回TCTで出展する造形サンプルのレベルで造形できる技術が確立している例はまだないと思います。
――世界でも屈指のレベルという事ですね!いつ頃から石英ガラスの研究に取り組まれたのですか?
私が大学院生の時から取り組んでいるので、かれこれ20数年近く前から取り組んでいます。当初は3Dプリンターは念頭にありませんでした。ですがとにかく「削りたくない」という基本的な方針で方法を模索していました。
というのも、私は博士論文で光学的性質である屈折率を計測する際、石英ガラスを削ってその後研磨する必要があり、非常に苦労しました。とにかく石英ガラスが非常に硬いので、ぜんぜん削れないんです。非常に苦労しました。師事していた恩師の森永健次先生が見るに見かねて、長野県の研磨職人の方を紹介して弟子入りを進めるほどでした。実際にしばらくその職人さんの下で修行させていただきまして、修行の後になんとか削れるようになったのですが、それでも石英ガラスを削るのは大変な作業です。
当時から石英ガラスを後加工なしで造形する方法を開発しなければ、いろいろな用途には展開できない、と課題を感じていました。いまでも「機能性ガラスを削らずに成形加工できる方法を構築する事が重要だ」と学生には指導しているほどです。
――研磨職人に弟子入り!そうでもしなければ加工できないほど手ごわい素材なんですね。いまはどんな用途に使われているのでしょうか?
石英ガラスは耐薬性の高さから、るつぼや半導体製造分野における部材、マイクロ流路として多岐に使われています。耐熱性の高さから水銀灯、殺菌灯、赤外線ランプにも使われています。透過率が高く光をよく通すので、太平洋を横断し海底に埋設されている光ファイバーケーブルなどにも使われています。多用途に使われているのですが、加工難易度が高いこともあり、多くのメーカーが独自の技術で取り組まれています。
例えば、特殊ガラスのメーカーは石英(クオーツ)のおおきな塊(インゴット)をつくってから、板状にスライスします。その後加工業者に渡して、研磨や用途にあわせた形状に加工します。ガラス細工を作るようにバーナーで加熱するのですが、石英ガラスの場合、通常の火力のバーナーでは火力が足りないので特殊なバーナーで加熱し、職人さんの手作業でフラスコやビーカーなどを造形する形です。
――もっと簡単に石英ガラスを造形するために、3Dプリンターで造形する前はどのようなアプローチを試されたのでしょうか?
スリップキャスト法という焼き物の技法からスタートしました。日本語では泥漿鋳込み法(でいしょういこみほう)というのですが、ろくろを回すのではなく、「石膏の型に液剤を流し込み、一部を残して液を排出(排泥)し、じっくり乾燥させたあと、焼き上げる」という方法で造形するアプローチです。
この着想は、私の恩師の森永先生に師事する中でうまれたものです。九州は古くから焼き物が盛んな土地柄で有名な窯元も多数あります。森永先生は焼き物がお好きで、地元の窯元にもよく足を運ばれていました。そんな中で職人さんとの交流の中で、伝統技法にも触れられていました。
また石英ガラスはシリカガラスとも呼ばれます。九州は半導体産業が盛んな土地でもあります。シリコンウェハーの切断時に大量の高純度シリコンの廃材がうまれます。シリコンに酸素を化合させると、シリカになります。この高純度シリコンの廃材を利用して地元発の新素材としてシリカガラスを世に広められないか、というテーマで研究を進めてきました。
――伝統産業のやきものと先端産業の半導体産業が石英ガラスでつながるんですね!おもしろい!
そうなんです。森永先生は通産省と産学官連携の国家プロジェクトを立ち上げられ、私も助手の頃に参加させていただきました。当時の成果として、プロジェクターのランプに石英ガラスを利用するといった成果につなげることができましたが、自在に加工するという点で課題を残していました。
森永先生は2002年にお亡くなりになったのですが、それ以来18年間、「石英ガラスを廉価に多用途に普及させるための造形法」は一貫して私の研究テーマでした。スリップキャスト法は、乾燥をじっくりおこなうために時間がかかりますし、微細な加工には向いていません。そんな中、液体樹脂をつかった3Dプリンターを見て「光造形で固めてしまえばできるのではないか!」と思い付き、さまざまな出発材料に取り組み、検証してきました。ここ数年はさまざな条件で造形材料を作っては、どの程度の品質がどのような配合で実現できるか徹底的に検証してきました。
――実際に造形する際に、こんな形状を実現したい、といったやってみたいものはありましたか?
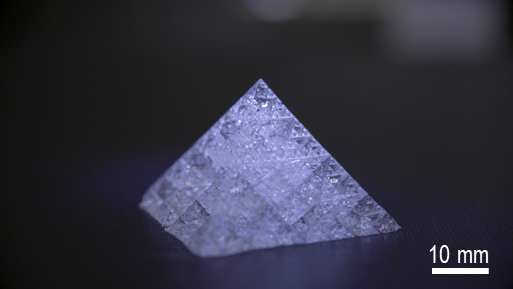
一番作りたかったものは、フラクタル構造のピラミッドです。三角形の中に3つの三角形を入れ込んだ構造体を連続して重ね合わせていくフラクタル構造は、従来の工法で石英ガラスを加工しようとしても不可能です。自由自在に造形できる証明という意味でも是非形にしたかった形状です。
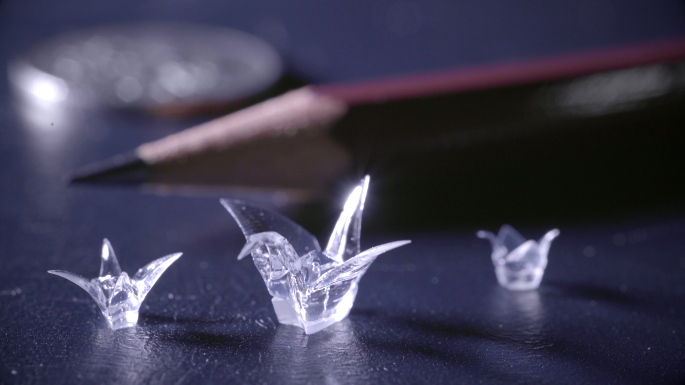
次に一般の方でも見てわかるものということで、折り鶴を作りました。
――石英ガラスを自由自在に造形できる技術の確立は、日本の快挙といっていいと思います!発表以来そうとう反響があったのではないでしょうか?
そうですね、産業関連のご相談や、樹脂をおもに扱っている材料メーカー、世界的な化粧品ブランドや自動車メーカーなど、すでに多くのご相談をいただいています。耐熱性、耐薬性、機械的強度という性能面でのお引き合い以外に、希少性という観点や透明度という観点で、アート分野や化粧品などの業界の方からご相談をいただいたのは驚きました。
――特許出願は九州大学からされているとのことですが、今後はどのように展開されますか?
私は研究者なので、あくまで研究を主体に置きたいと思っています。大学としては、大学発ベンチャーとして育てたいという意向もあり、展開を検討をしているところです。大学発のベンチャーが誕生すれば、その企業にライセンスを供与して活動していくという事になると思います。
液体材料の開発をおこなって、その販売を行う。必要に応じてサービスビューロとして造形も受託するなどの展開があると思っていますが、今は「こんなことをやりたい」「こんなことができないか」といったお話をできる限り幅広く伺っていきたいと思っているところです。
――今回のTCT Japan 2020ではどんなことを期待されていますか?
ブースには、石英ガラスを実際に造形したフラクタル構造の造形物、将棋の駒、折り紙の鶴の形の造形物をはじめとした造形サンプルをたくさんご用意しています。実際にご覧いただき石英ガラスの優れた特徴と将来性について知っていただきたいです。
また、企業のノベルティーで石英ガラス製の記念品を作りたい、楽器や自動車をつくりたいといったお話でもいいですし、こんな特殊な装置につかえないか?といったお話でもいいです。いま考えているアイディアを沢山お伺いしたいと思っています。アイディアをもった方々との出会いを期待しています。
***
関連記事
関連リンク
2019年のシェアラボニュース創刊以来、国内AM関係者200名以上にインタビューを実施。3Dプリンティング技術と共に日本の製造業が変わる瞬間をお伝えしていきます。