シェアラボ編集部では、外野の希望的観測ではなく、受託製造の体制を整え、受託仕事として事業を展開するサービスビューロに実感を聞いていくべく取材を行っている。今回は3DiH(3D innovation Hub)と銘打ってアライアンスを組み活動を行うJMC社を取材した。3Dプリンターに1999年から取り組み、上場企業にまで育て上げた株式会社JMCの渡邊大知社長に取り組みの背景、活動の現在と今後の展望に関してお話を伺った。
目次
1999年から3Dプリンターで造形受託を行う老舗サービスビューロ JMC
シェアラボ編集部:JMCさんは光造形主体のサービスビューロとして、上場されていますが、簡単に自己紹介をお願いします。
渡邊社長(以下、 渡邊):私たちJMCは光造形主体で3Dプリンターで受託造形事業を行っています。1日あたり30枚から50枚、時にはそれ以上の図面をさばきます。その多くは試作品です。またCTスキャンで造形物の非破壊検査にも取り組んでいます。作って検査してというところまで自社で一貫して行うことができます。
そもそもの始まりは私が1999年に3Dプリンターで受託造形事業を始めたのがきっかけです。かなりの老舗のサービスビューロだと思います。2013年にアメリカのオバマ大統領がメーカーズムーブメントの中で、3Dプリンターならなんでも作れるという印象を広めてから、市場は一気に熱くなり、その後急速に冷えてしまったのも見ていますし、3Dプリンターという言葉が独り歩きする中で、地道に取り組みを続けてきました。
この10年で産業用3Dプリンター市場は4倍に伸びたが、まだまだ200億規模
シェアラボ編集部:実際に実ビジネスとしてお取り組みになる中で、市場は広がってきましたか?
渡邊:この10年で50億円が200億円になったかもしれませんが、大変小さい市場であると感じています。3Dプリンター市場に関心を持っている企業は多いですが、撤退する企業も多く、毎月のように装置や事業の売却話が舞い込んできます。常々市場の規模を広げなくては、と感じていました。
シェアラボ編集部:何が課題になっているんでしょうか?
渡邊:JMCは試作を中心に3Dプリンターで造形を行っているのですが、毎年のように様々な企業から3Dプリンターの現状や実際のところに関して相談が来ます。「実際のところどうなの?造形したものの物性はどんな感じ?」といった質問です。産業用3Dプリンターメーカー各社の事例は海外事例ばかりだし、出してくる材料スペックは各社指標がばらばらで単純な比較も困難。社内でも導入しているけれども、なかなかうまくいかない部分もある。そこで実際に造形を行っている企業にヒアリングしようとなるようです。
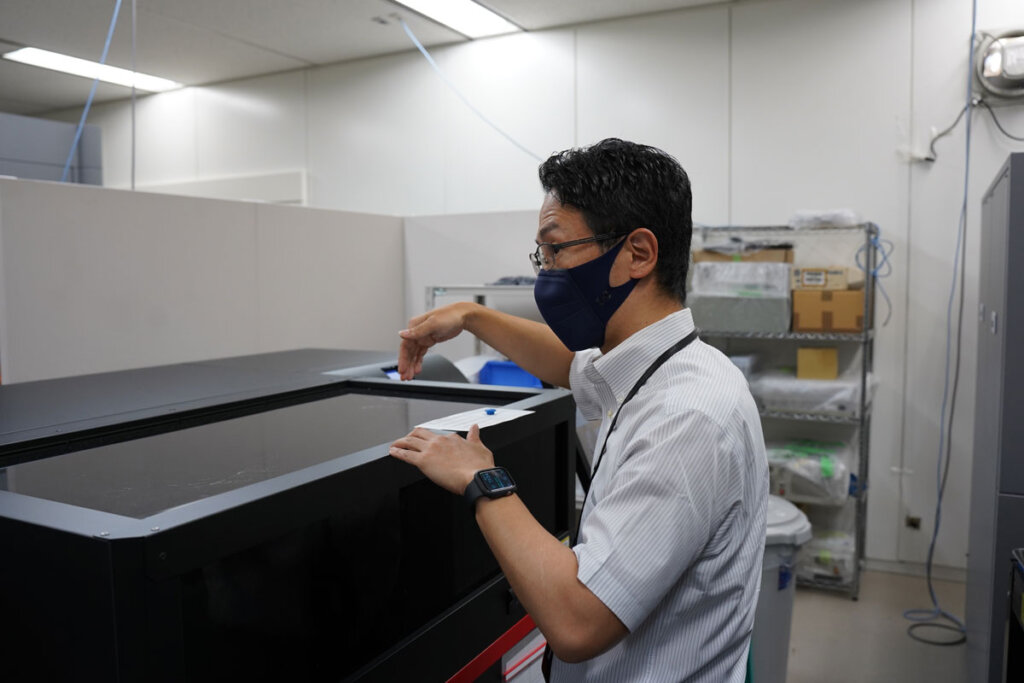
シェアラボ編集部:結構な頻度で相談がくるんですね。
渡邊:そうですね。いろいろな会社さんからの相談が来ます。3Dプリンター業界でも横のつながりはありまして、親交を深めていた八十島プロシードさんとみんな3Dプリンターの現状がわかっていないので相談にきますよね、と話をすることがありまして、そうだね、とお互いに頷けるところが多かったんです。
みんな同じような課題で悩んでいるなら、こちらからお知らせする活動をしてはどうかということで、原田車両設計さんもお誘いして、始めたのが3DiHです。
シェアラボ編集部:素早く試作品を造形するJMCさんと、中量量産にも対応している八十島プロシードさん、設計に強みをもつ原田車両設計さんとそれぞれ特徴を活かした情報発信ができそうですね。具体的にはどんな情報を発信しているのでしょうか?
渡邊:先日は八十島プロシードさんの工場見学をオンラインで開催しましたが、いまこんな装置があり、こんな部品が作れるという実態を紹介しました。八十島プロシードさんには30台以上の工業グレードの3Dプリンターがあります。実際にここまでできるというのをリアルにご紹介できたと思います。
また先日、比較的エントリーモデルの装置に限ってですが、複数メーカーの出している装置を紹介するコーナーも設置しました。どんな装置があって、どうやって使い分けたらよいかというご相談も多いので、それにこたえる形で掲載しています。
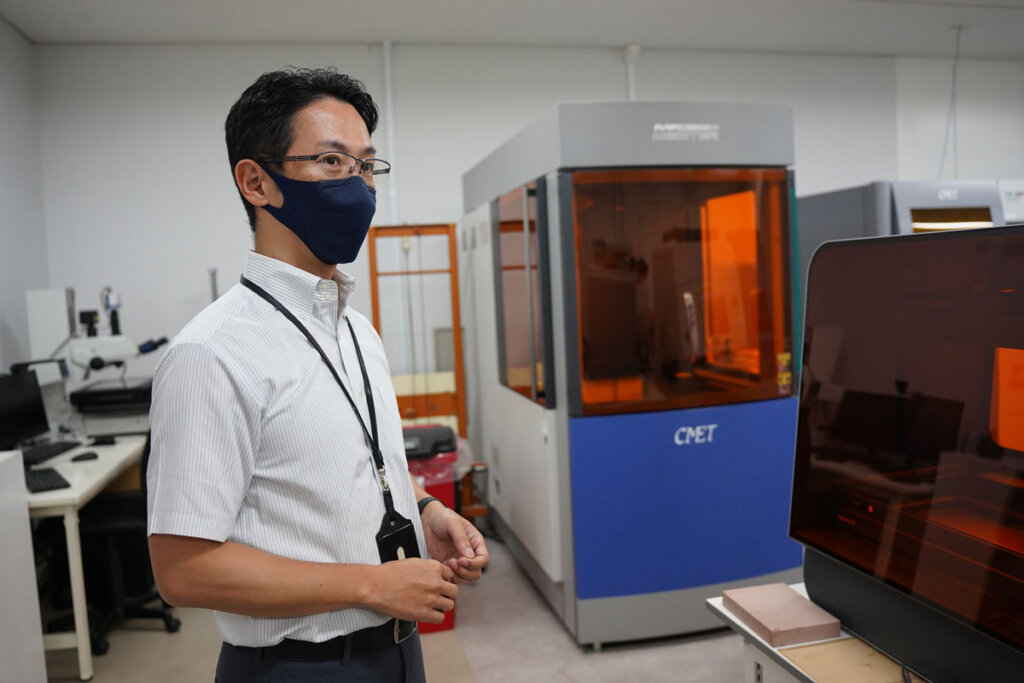
シェアラボ編集部:シェアラボ編集部でも八十島プロシードさんの工場見学は参加させていただきました。結構フランクな形で紹介されていて大変興味深く拝見しました。
渡邊:数万円の卓上3Dプリンターも産業用3Dプリンターも一緒くたに見られてしまう風潮があるんですが、3Dプリンターは魔法の箱ではありません。なんでも高い品質で造形できる装置ではないんです。
3Dプリンターは造形に高い自由度があります。一方で量産に必要な再現性という面では他の工法には劣ります。大型の光造形方式の装置の場合、材料に液体樹脂を使うのですが、レーザーで硬化させるタンクの中には数百リットルの材料が入っています。そしてその材料はレーザーで熱や光を受けるなかで絶えず劣化していきます。同じ条件の材料に同じ条件の光を当てる、ということができないわけです。劣化していく材料に対してどのように調整をかけていくか。装置を操作する側の経験やノウハウによって結果が変わってくるのです。
シェアラボ編集部:新機種発売の際は、私たちもメーカーさんにお話を伺うんですが、実際に3Dプリンターを使っている製造現場で何が起こっているかは、伺う機会も少なくて、なかなか情報が出てこないですよね。

渡邊:そうかもしれません。実態をよく知らずに、3Dプリンターで何でも作れると信じている人もいます。そんなことできないのに、ということを平気で語る人がいるせいかもしれません。3Dプリンターは自由度が高いけれど、量産時に求められる再現性に劣る装置です。トレードオフなんです。でも量産が可能で、誰でもできるし、儲かると言っている人が絶えません。だからこそ、3DiHのような取り組みに対して、気になることを相談してもらえたら、実態をきちんと踏まえたお話ができるんじゃないかと思います。お問い合わせフォームで相談いただければ、参画している3社で協議して、きちんとお返事をするようにしています。
シェアラボ編集部:夢を語りすぎな人が多いというお話は、私たちメディアにとっては耳が痛いところです。新規ネタに飛びついて『3Dプリンターすごい!』と言いがちな面はたしかにあるので。夢を語る一方で、現実を踏まえた冷静さは必要ですよね。現場の皆さんの実感値をちゃんと伝えていくので、もし変なことをいっていたら教えてください(汗)
3Dプリンター機種選びが難しい理由
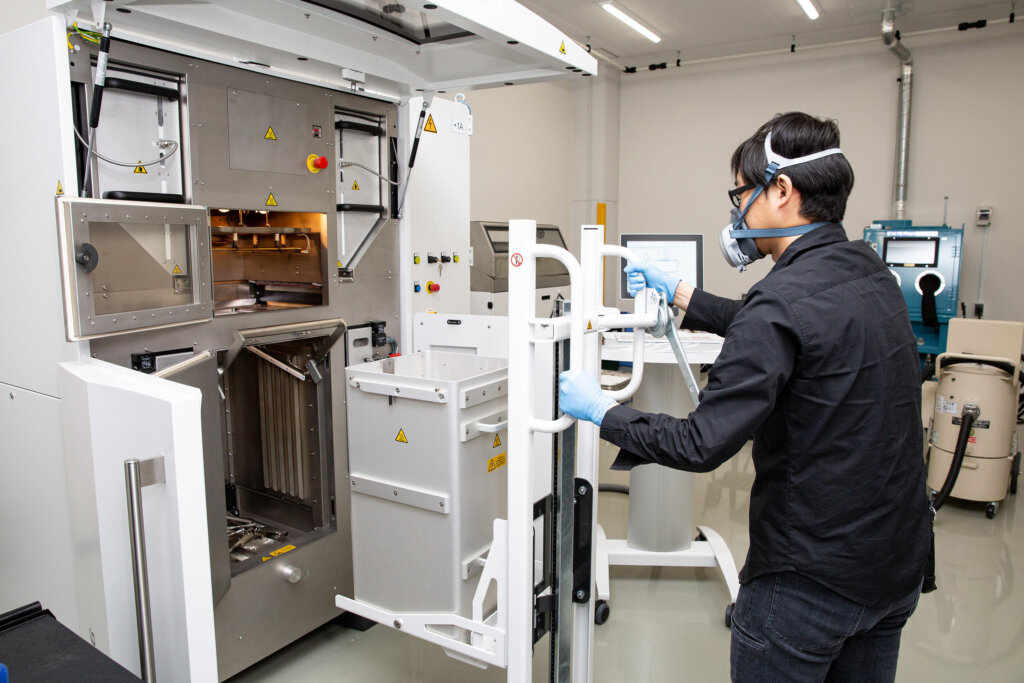
渡邊:私たちも装置販売を行っていましたし、最近も3DiHのサイト上でおすすめの装置をご紹介し始めました。ですが実は、しばらくの間、私は装置販売をやめていたんです。というのも、私たちから装置を買って受託製造事業を始める会社さんは私たちと競合になってしまいます。すると同じような装置を使っているため、私たちのほうが営業力も技術力もあるので、競争に私たちが買ってしまうんです。
すると1年たたないうちに、うちに装置を中古で買ってほしいとか、営業譲渡の相談に来てしまいます。せっかくのご縁でお取引きしたのに、廃業させちゃうのが悪くて。それ以外にも定期的に、事業を買ってほしいという相談がきます。うまくいっていない企業は少なくありません。
それに高額の装置を導入すればちゃんと生産がうまくいくかといえばそんなこともありません。成功している海外の事例を実際に視察に行くと、海外の工場では多くの台数を並べてリスクヘッジしています。2台装置を導入しても装置に不具合がでることがある。だから4台入れる。現実的にそう対処しているんです。
うまくいかない場合、多くの人は工作機械と比較して、操作する自分が間違っている、もっと違うやり方をすればうまくいくはずだと考えます。数千万円の装置を入れてできないでは済まされないので、そう考えちゃうんです。でも3Dプリンターの場合は他の工作機械と比べると技術の成熟度が浅く、装置側のトラブルで上手くいかないというケースが起こり得ます。新しいものであるからこそ、こういうことがあるんです。つまり、無料でおいてくれというのは、立ち上げノウハウを作ってくれということと同義なんです。
だから私たちは、無料でいいから導入してほしいと言われても、断ります。実際に自分たちが導入したい装置しか導入しません。それだけちゃんと産業用の3Dプリンターを使いこなすにはノウハウが必要です。そこで収益を上げるのはさらに一工夫必要です。
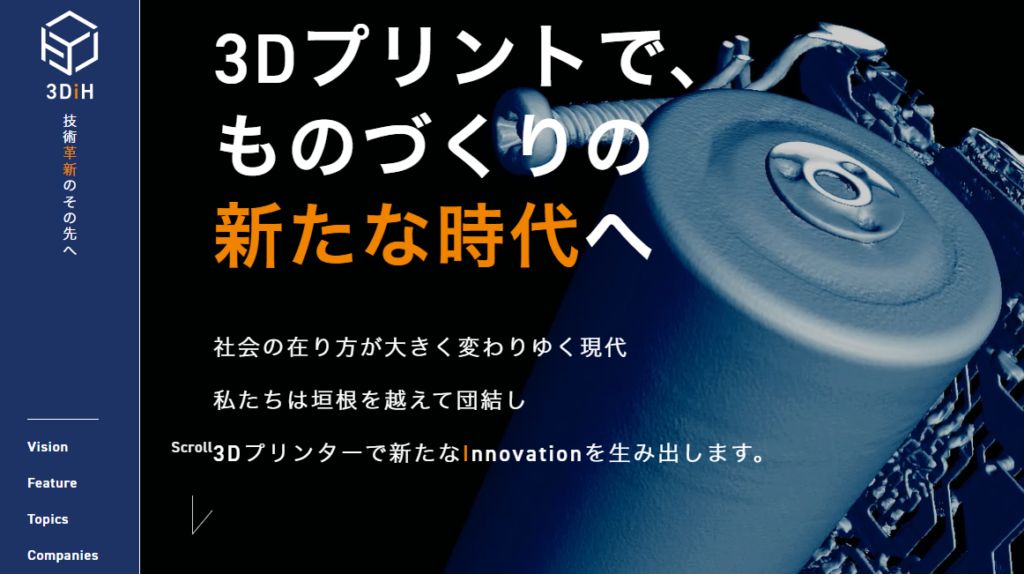
シェアラボ編集部:でも今回装置の紹介を始められましたよね?なぜですか?
渡邊:やはり触ってみて、実感をしていただくことが大事だと思うからです。エントリーモデルの3Dプリンターを導入して、実際に試作を行ってみる。そこでできること、できないことを知っていただき、どれくらい稼働させられるか実感していただくことが必要と思います。自社内で試作を行うだけであれば、エントリーモデルの装置と私たちのようなサービスビューロへの発注だけで事足りるかもしれません。それでも数千万円の装置を買う必要があるほど社内需要があるのであれば、目的に即した装置を導入するべきです。やってみないとそのあたりが見えてこないと思いますので、まずは比較的廉価な装置のご案内をはじめました。
選び方のコツは経験者に聞くこと
シェアラボ編集部:なるほど。いきなり高額な装置を導入してもうまくいかないから、まずエントリーモデルを導入して、あるべき姿を考えたらどうか、という意図だったわけですね。
渡邊:そうですね。弊社は光造形方式の3Dプリンターが複数種類、稼働しています。CMETの3DプリンターとFormlabsの3Dプリンターで同じ光造形方式でも特徴がまるで異なります。どんなものを作るときにどの装置のどの材料がよいのか、私たちは毎日現場でさまざまな形状を造形しているので、正しい使いかたがわかります。使い分けているんです。
また鋳造の巣を検査するための非破壊検査用CTスキャナーも設置しています。自動車メーカーさんがレース部品の検査や不良品の原因究明を自社ではなく、私たちに検査を依頼してくるほど、信頼性が高い装置であり、オペレータを備えています。作って非破壊検査ができる体制があるんです。
こうした製造して試験もできる環境を持っていて、用途によって使う装置を的確に判断しながら毎日操業している経験があるからこそ、用途にあった装置を導入したり、今後どのような取り組みを行うべきかがわかってきます。
シェアラボ編集部:3Dプリンターの造形方式も様々ですし、同じ造形方式の中でもさらに細分化していますよね。どれも特徴があって、単純な上位互換というわけではないようですし、自社でどこまでそろえて、できない部分をどう外部と連携するかという視線は大事になってくる気がします。
渡邊:そういう意味でも、どうやって購入する3Dプリンターを選べばいいか、という質問には簡単な答えはありません。どんな用途で使うのか、自社内でどこまでそろえ、できない場合に外部をどの程度活用できるかによって変わるからです。
弊社でも取得していますが、航空関連の認証では、どの装置を、どの材料を使って誰がどのような手順で操作するのか(4M:Man Machine Material Method)がセットで審査されます。同じ機種でも違う個体で作っては審査がおりません。それほど厳しく専用の製造装置を具体化していきます。そういった最終部品製造用途で使う場合といろいろな形状の試作をスピーディーに用意する場合で大きく要件が異なります。
シェアラボ編集部:自社で全部できればもちろん秘密保持も容易ですが、ノウハウ蓄積や設備導入コストが大変そうです。
渡邊:装置と同じように重要なのが材料です。3Dプリンターの材料でABSライクという材料があります。ABSに近い物性を示す材料という意味で、ABSライクなのですが、メーカーによってはABS/PPという記載の場合があります。ABSにもPPにも似ている材料という意味なのですが、ある物性がABSに近いからABSライクと呼んでいるだけなんです。他の数値をみると全然ABSではない。材料販売業者からみると、とんでもない材料ということになります。こうした材料を同じ基準で比較した実際の数字を持っているサービスビューロは少数です。いろいろな装置を実際に使って造形し、検査したことがないと持っていない生の数字なのです。うちはこの機種だけしかないから、と言っていると対応できないわけです。
シェアラボ編集部:みんな同じことで悩んで同じ検証をやるのは無駄なような気もしますね。
渡邊:だから先ほど例にあげた材料の実際に物性や最適な造形方法に関して、私たちは情報を発信しようとしています。メーカー各社の材料を同じ基準で評価できる数字をもっているのは私たちの強みです。その強みを活かして小さな市場で勝つのもよいのですが、業界のすそ野を広げていけばさらに市場は大きくなります。そういった活動を3DiHでは行っていきたいと考えています。
毎日受託造形を行っているサービスビューロに装置導入を相談できるのは魅力
毎年3Dプリンターの展示会に行くたびに、新機種があらわれ、新しい造形材料が追加される。以前の7倍造形速度が速いだったり、2倍の造形サイズを誇るだったりと装置や技術が進歩していく。そんな姿を見てついつい夢見がちになるが、実際に何をどのように造形しどのようにビジネスに活用していくかが大切であり、トラブルなく現場に落とし込んでいくことが重要になる。
他社の先行事例にヒントを得ながら自社でどんな成果を実現していくか。そんな際に、実際に受託製造で実績を出している企業のアドバイスを得られることは大きなメリットだろう。メーカー各社もユーザー企業の声をとりあげた事例を作ろうとしているが、秘密保持の壁は高い。サービスビューロからの情報発信や、その情報を踏まえた実践的な相談ができる場として、3DiHを活用できるのであれば調査や検討の時間を大きく削減できるかもしれない。
2019年のシェアラボニュース創刊以来、国内AM関係者200名以上にインタビューを実施。3Dプリンティング技術と共に日本の製造業が変わる瞬間をお伝えしていきます。